Additive Manufacturing in Industrial Production
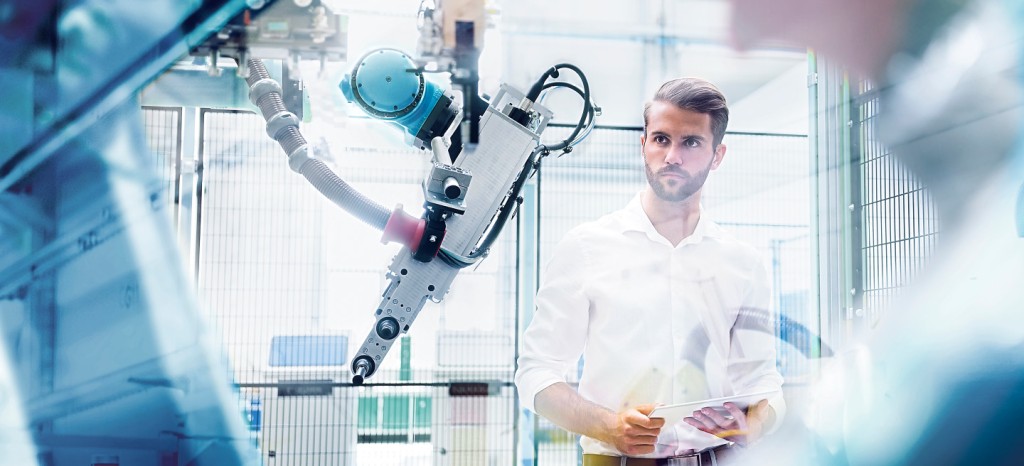
Table of contents
- Elements of the AM Value Chain
- Design Phase – Paradigm Shift in Design
- Raw Materials – New Possibilities in the Production
- Manufacturing Process – Integration of New Types of Machines and Processes into the Production
- Post-Processing – Optimization of Surfaces or Material Properties
- Product – Functional Optimization
- Operation – Commissioning and Lifetime Monitoring
The use of additive manufacturing processes, usually referred to as "3D printing," is becoming increasingly more established in many areas of life and in many industries. Additive manufacturing (AM) is the layer-upon-layer manufacturing of components based on digital 3D model data. In contrast to conventional manufacturing processes, the component is created by bonding individual powder layers or material layers sequentially on top of each other.
Of the wide variety of AM technologies, metal-processing technologies have the greatest relevance for manufacturing pressure equipment components. Chief among those are the so-called direct energy deposition technologies (e. g. laser powder buildup welding or wire-based Wire Arc Additive Manufacturing (WAAM)) and the powder bed fusion laser-based processes (PBF-LB). While in the former processes the component is created bead by bead by buildup welding, in the latter process, the desired three-dimensional shape is achieved through the selective melting and fusing of a powder layer.
Elements of the AM Value Chain – a New Value-Adding Process
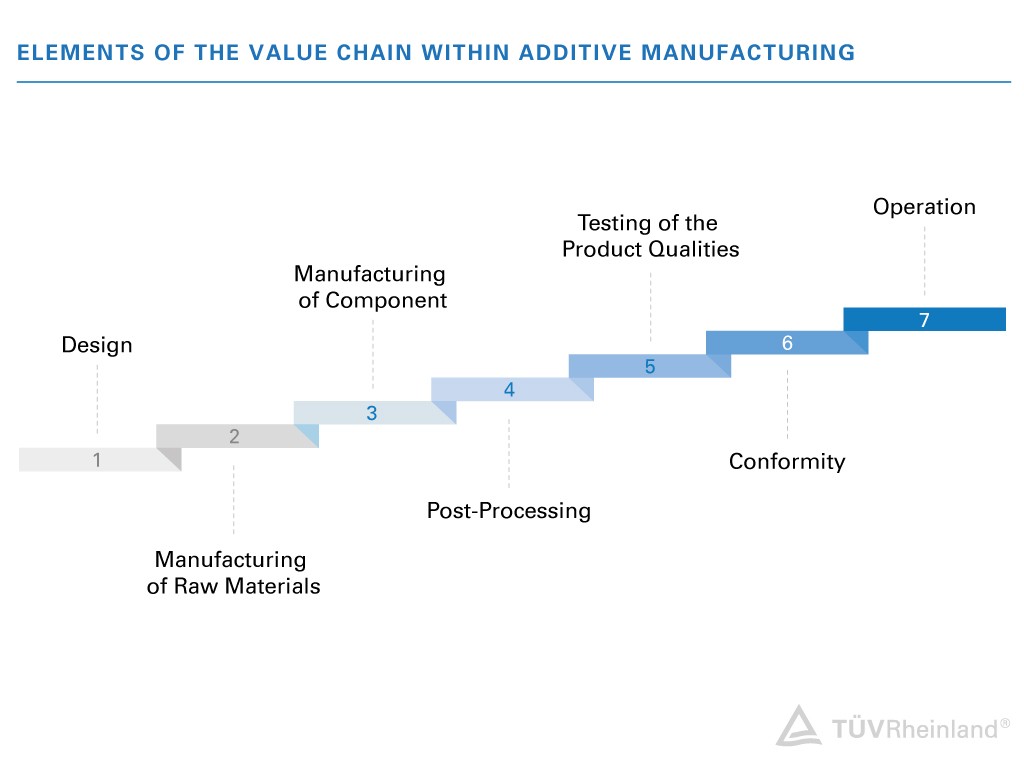
Under the Pressure Equipment Directive (PED 2014/68/EU), there is currently no uniform set of regulations that applies to the production of pressure equipment made by additive manufacturing. In order to still produce compliant pressure equipment, related standards from other industries and processes are used where appropriate.
However, as there are no harmonized standards for pressure equipment, the effort involved in designing and testing is very complex. This represents a great challenge for the large-scale use of AM in pressure equipment manufacturing. It is therefore even more important that you have a partner at your side who is familiar with the relevant standards. We have comprehensive experience and expertise along the entire AM value chain and use our extensive technical knowledge to support you.
A certified higher-level management system is critical in this context to systematically drive the company's success through continuous and efficient improvements. With regard to a specific product, a certification according to PED 2014/68/EU and AD2000 can be performed as a combined certification. As part of the system certifications, the manufacturing sites undergo a general audit. This way, we cover all relevant quality assurance procedures for the entire AM value chain (production process).
Design Phase – Paradigm Shift in Design
Additive manufacturing (AM) is revolutionizing the design and production of components. A new challenge for designers and developers are the methods and design rules aggregated under the term Design for Additive Manufacturing (DfAM) that allow an AM-optimized design (lattice structures, generative design, topology optimization, thermal simulations, etc.). The rules also depend on the properties of the equipment, such as build volume, printing technology (Metal 3D, FDM, SLS, etc.) and the raw material.
The main advantage is the extensive freedom in terms of the design. Components can be optimally adapted to the functional requirements, resulting in completely new, function-integrating designs that justify the associated cost that is currently still higher than with conventional methods. The replication of a conventional design is also possible, but because of the higher cost and longer time, it is currently not an advisable use of this new technology.
Pressure equipment that falls within the scope of PED 2014/68/EU often requires a design examination by a Notified Body such as TÜV Rheinland (exception for Cat I, II modules A, A2, D1, E1). During the design examination, our experts can also evaluate the particular features of the AM design and AM production such as complex geometries, porosity, internal stresses in the design phase and more, which is done by performing FEM simulations for example.
For a subsequent welding-related use of the pressure equipment within the operator's existing equipment technology, our welding technology experts can be involved at an early stage in the planning process.
Design Examination and Conformity Assessment According to PED 2014/68/EU
Raw Materials – New Possibilities in the Production
The manufacturer/supplier of the raw material/powder will be reviewed with regard to the quality requirements for their product including production safety. In this process, the human factor, i. e. the knowledge of and the experience with the materials plays just as important a role as the production equipment, which must be periodically calibrated and tested. The pressure equipment manufacturer is usually closely involved in the material production process. The materials manufacturer is responsible for ensuring that the requirements with regard to the material are met. The material specification defines the technical specifications required for the design and validation of the material properties.
The pressure equipment component manufacturer enters the AM value chain as a new player. He acts as the interface between the manufacturer of the raw materials and the pressure equipment manufacturer and serves as an extended workbench in the production of the component.
Certification as a Materials Manufacturer or Pressure Equipment Component Manufacturer
If there already are existing certifications, the specifics of additive manufacturing according to the above table can be included by extending the scope of the particular certification.
Manufacturing Process – Integration of New Types of Machines and Processes into the Production
3D printers must be integrated into the already spatially optimized production line. It is therefore necessary to set up dedicated facilities, because of the required cleanliness for powder bed fusion processes, for example.
The technologies used in the new types of machines – such as lasers and electron beams – and the type of materials introduce new potential safety risks to the production line. For many manufacturers, the use of metal powders creates new challenges for the occupational safety and environmental protection of their materials logistics.
The concept of sustainability is integrated into additive manufacturing through the fact that unused raw materials can be reused, provided they meet the quality requirements of the specification.
In the qualification of the manufacturing process, the manufacturer provides documented proof that components with defined material properties can be produced in a reproducible quality. This is first of all based on the build volume qualification, where mechanical-technological and geometrical properties are described as a function of the process parameters and the position or orientation in the build chamber or on the build platform.
Post-Processing – Optimization of Surfaces or Material Properties
In contrast to conventional (subtractive) manufacturing processes, components in additive manufacturing must be detached from their build plate, and any support structures, thermostructures and excess metal powder that may have been necessary for the manufacturing process must be removed. A heat treatment or surface finishing are other possible production steps that may follow.
Transfer of Marking, Certification for Heat Treatment Furnaces
Product – Functional Optimization
If all required rules of AM design are followed, the result of your new manufacturing process will be a novel product (component) that is functionally superior to a comparable conventionally produced product, saving you assembly costs, material costs and space, and also offering new functionality or greater efficiency.
Operation – Commissioning and Lifetime Monitoring
AM pressure equipment is usually integrated into complex systems and thus often welded to non-AM pressure equipment such as pipes. This may result in special testing requirements over the life cycle of a plant that requires monitoring under the German Ordinance on Industrial Safety and Health (BetrSichV). TÜV Rheinland assists plant operators with developing testing concepts and with lifetime monitoring through non-destructive testing or condition monitoring while taking into account the special requirements for AM pressure equipment.
Our Services
Additive manufacturing allows the production of pressure equipment with complex structures and improved properties. However, in many areas, there still are no harmonized standards for the testing and certification of additive manufacturing.
We support you as a manufacturer in all issues related to the conformity of the pressure equipment and the material technology and testing technology of metal pressure equipment. Take advantage of our expertise as a Notified Body under the Pressure Equipment Directive PED 2014/68/EU. Have your management system or your product tested and certified with regard to AM-specific requirements. Our accredited laboratory (DIN EN/ISO IEC 17025) offers comprehensive analysis and material testing methods for safely assessing your pressure equipment and for placing it on the market.
Your Global Partner with Technical Expertise and Great Service Orientation
As a globally positioned testing and certification service provider, we are familiar with all relevant standards related to additive manufacturing/3D printing worldwide. Together with regulatory authorities and major industrial companies, we are part of committees that work on the development of these standards. Our experts monitor the development of standards for you at all times.
Our excellent reputation as an independent body will ensure that the safety, quality and conformity of your products and processes are recognized worldwide. In addition, our team of additive manufacturing experts has in-depth technical knowledge about materials, manufacturing technology and industrial applications.
In our partnership with you, service is our top priority. We work together with you to find customized solutions that are tailored to your specific task and your industry.
Our expertise in additive manufacturing/3D printing starts with the cyber security of your design processes, includes testing of materials and machinery, occupational safety and compliance of equipment and processes, as well as testing of products and services for global market access. In short, with us you will get a true one-stop shopping experience and will be supported by knowledgeable experts with a sound industry expertise who speak your language.
Contact
