Reduzir a duração de suas paralizações programadas e minimizar os riscos de paradas não planejadas
Durante uma parada, o foco é retomar o processo de produção o mais rápido possível e, ao mesmo tempo, reduzir os custos de manutenção. Portanto, são necessários trabalhadores experientes e qualificados para identificar a condição atual do ativo com a ajuda de métodos END(A) apropriados. O objetivo é resolver o problema de forma rápida e econômica, para que a produção possa ser reiniciada o mais rápido possível.
Supere desafios específicos durante as paradas da fábrica
Os proprietários e operadores de ativos enfrentam desafios especiais durante a fase de desligamento porque a produção foi interrompida e os equipamentos críticos devem ser inspecionados e reparados adequadamente. Aqui estão os principais desafios comuns para os proprietários e operadores de usinas:
Quanto mais tempo a fábrica ficar parada, maior será a perda de tempo de produção e de rendimento. É por isso que o objetivo dos proprietários e operadores de ativos é retomar a produção o mais rápido possível. O tempo de inatividade do equipamento pode ser minimizado pelo planejamento ideal das atividades de paralisação. A abordagem de Inspeção Baseada em Risco (RBI) é comumente usada para otimizar as frequências de inspeção e reduzir a exposição ao tempo de parada.
Durante uma parada não planejada, a produção é interrompida de forma não intencional. Qualquer mau funcionamento do sistema pode levar a graves danos à saúde, à segurança e ao meio ambiente (HSE). Uma boa preparação das atividades de parada, incluindo a definição dos melhores métodos de inspeção, ajudará a executar o número mínimo de inspeções, proporcionando o mais alto nível de detecção de pontos fracos e defeitos em serviço, reduzindo, assim, os riscos de incidentes e paralisações não planejadas.
- A realização de qualquer inspeção no interior de uma embarcação acrescenta riscos significativos à saúde e à segurança e exige custos extras de preparação e gerenciamento.
- Realizar qualquer inspeção interna em vasos e tanques de pressão acarreta riscos significativos à Saúde e Segurança, além de exigir custos adicionais de preparação e gestão. A Inspeção Não Intrusiva (NII) pode ser a solução para este desafio.
- Evitar a drenagem, a purificação e a limpeza desnecessárias dos vasos, que não requerem manutenção, ajudará a melhorar as metas de sustentabilidade.
- As paralisações não controladas podem causar danos à reputação da marca corporativa e altos pagamentos adicionais devido à responsabilidade financeira. Além do medo de perder o produto e os ativos físicos, o foco principal é garantir a saúde de todos os funcionários envolvidos e do público (por exemplo, em caso de riscos de explosão).
No caso de uma parada planejada ou não planejada, nós o ajudamos a retomar a produção o mais rápido possível e a cumprir as precauções de segurança de acordo com as normas. Portanto, oferecemos um amplo portfólio de métodos de END convencionais e avançados, para que você possa retomar suas operações o mais rápido possível.
Nossos métodos de END: Possibilitam a continuidade de sua produção, proporcionando inspeções que economizam tempo e custos
Dependendo da degradação esperada, da geometria, da espessura e do tipo de material, oferecemos métodos convencionais e avançados de ensaios não destrutivos adaptados às suas necessidades. Alguns dos testes são realizados no lado interno de um objeto a partir do interior de um vaso, mas alguns testes podem ser realizados do lado de fora do vaso usando a abordagem de Inspeção Não Intrusiva (NII). Dê uma olhada nas diferentes aplicações e na nossa linha completa de técnicas de inspeção:
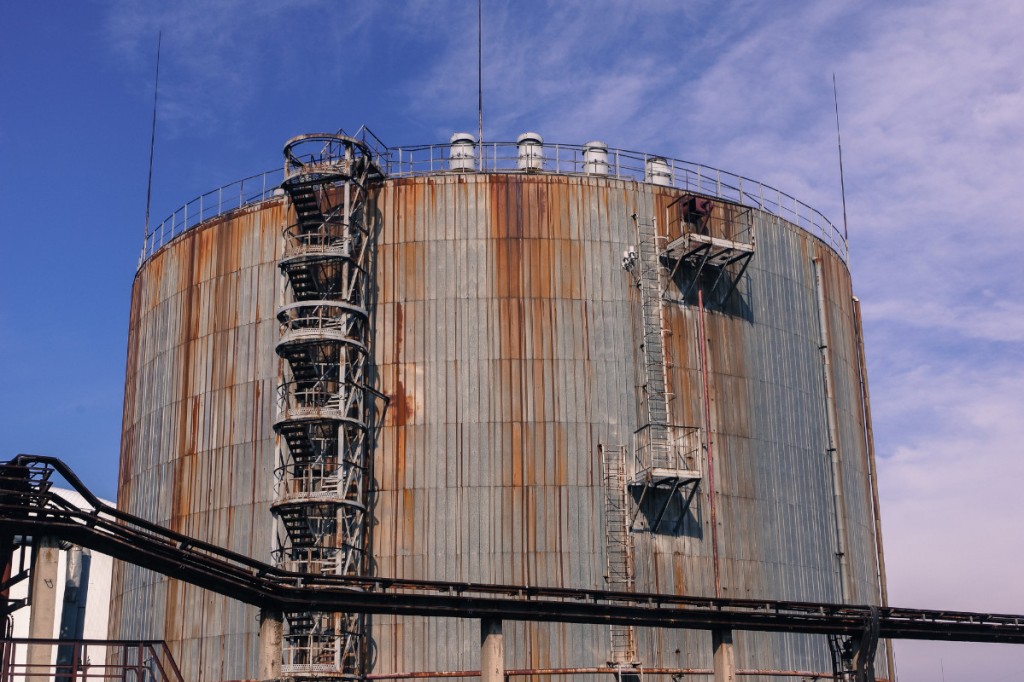
Métodos END para detecção de corrosão
A corrosão é um problema que afeta quase todos os grandes setores e pode se manifestar de várias maneiras. Há diferentes formas de corrosão, como afinamento da parede, corrosão por pite ou corrosão sob isolamento (CUI). Esses efeitos podem causar reparos dispendiosos e riscos à segurança. O que é necessário é um plano eficaz de inspeção de testes não destrutivos que detecte anomalias corrosivas em um período de tempo mais curto e em uma ampla variedade de equipamentos.
Veja abaixo um amplo escopo de nossos métodos convencionais e avançados de Ensaios Não Destrutivos para detecção de corrosão:
Veja abaixo um amplo escopo de nossos métodos convencionais e avançados de Ensaios Não Destrutivos para detecção de corrosão:
- Teste visual remoto (corrosão, degradação de material) usando endoscopia: Determine a qualidade dos componentes remotamente.
- Teste Ultrassônico de Longo Alcance (LRUT) / Onda Guiada: Detectar corrosão e erosão de tubos sob isolamento
- Pulsed Eddy Current (PEC): Avalia a condição de componentes de aço de baixo carbono penetrando através de camadas de isolamento e revestimento que não são magnéticas e não conduzem eletricidade (ou seja, sem remover o isolamento ou o revestimento).
- Vazamento de fluxo magnético (MFL): Detectar corrosão e corrosão em estruturas de aço magnetizando o material (por exemplo, tanques de armazenamento).
- Inspeções de tanques com SLOFEC: Detectar corrosão e corrosão em estruturas de aço magnetizando o material (por exemplo, tanques de armazenamento).
- Exame radiográfico (RT) Exame de Raios Gama (inspeção de perfil): Determina a espessura exata e detecta descontinuidades no material que está sendo exposto no filme ou na chapa digital.
- Exame ultrassônico (UT): Determinar com precisão a espessura dos componentes para comparar a espessura real do material com o nível de espessura projetado ou aceito.
- Ensaio por Ultrassom (UT) com crawler: Robôs do tipo crawler permitem acesso facilitado a componentes de difícil alcance, possibilitando a realização da inspeção por UT sem a necessidade de andaimes ou plataformas de acesso.
- Exame de Phased Array (PA) da solda (identificação): Um método de UT que oferece uma taxa de detecção mais alta de defeitos volumétricos e a possibilidade de salvar dados para revisar os resultados posteriormente.
- Exame de Difração de Tempo de Voo (ToFD) da Solda (dimensionamento): Detectar e dimensionar a profundidade e a altura de falhas de fusão, rachaduras, etc. em uma construção soldada, independentemente de sua orientação.
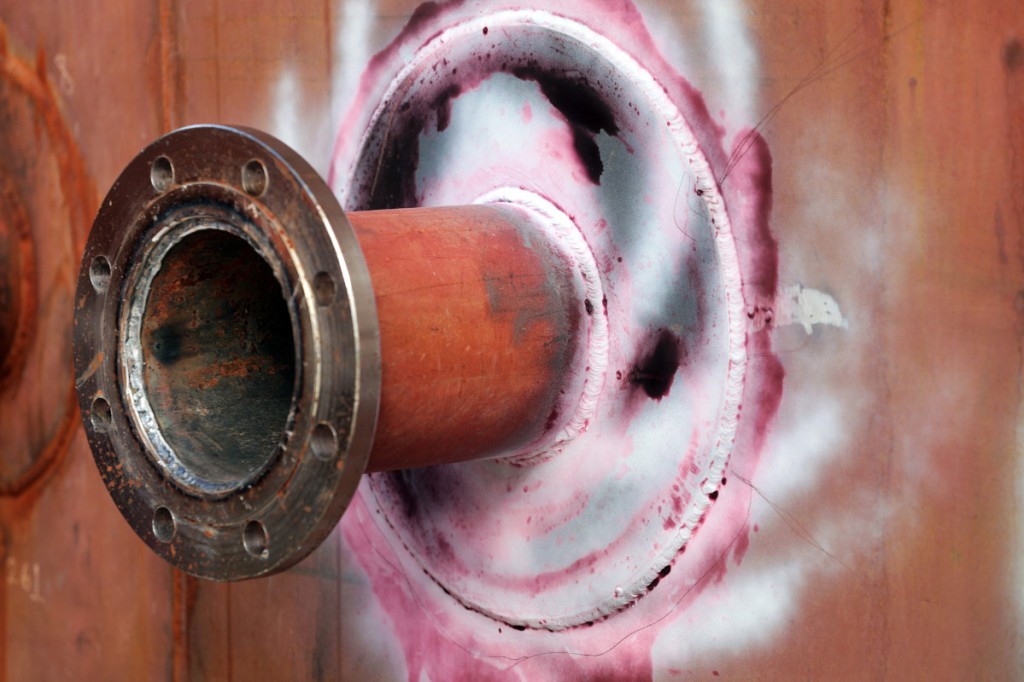
Métodos END para detecção de trincas e vazamentos e identificação de danos na superfície
O teste de trincas refere-se a vários métodos para a detecção de trincas e vazamentos em materiais e a consequente avaliação da segurança dos componentes relevantes, por exemplo, vasos de pressão, tubulações e componentes do setor petroquímico, de processos ou de gás. Os métodos de superfície são usados para identificar defeitos superficiais e próximos à superfície, como rachaduras e porosidade superficial. Mesmo os defeitos de superfície aparentemente menores, se não forem tratados com rapidez suficiente, podem, por exemplo, resultar em danos generalizados a qualquer rede de tubulação.
Dessa forma, é necessário um END regular para garantir a integridade dos ativos e evitar acidentes. Fornecemos os seguintes métodos para detectar possíveis rachaduras, vazamentos e danos à superfície:
- Medição de Campo de Corrente Alternada (ACFM): Detectar rachaduras por meio de pintura ou revestimento (amplamente utilizado para inspeções submarinas).
- Teste de partículas magnéticas (MPT/MPI): Detectar descontinuidades em materiais ferrosos.
- Teste de penetração de corante (DPT/LPI): Localize defeitos de quebra de superfície em todos os materiais não porosos.
- Teste de vazamento de caixa de vácuo em pisos de tanques de armazenamento: Detectar a localização de vazamentos.
- Teste de emissão acústica (AET): Detectar deformações metálicas crescentes, rachaduras, corrosão e defeitos em um estágio inicial.
- Exame de PA (Phased Array) da solda (identificação): Um método UT que oferece uma taxa de detecção mais alta de defeitos volumétricos e a possibilidade de salvar dados para revisar os resultados posteriormente.
- Exame de Difração de Tempo de Voo (ToFD) da solda (dimensionamento): Detectar e dimensionar a profundidade e a altura de falhas de fusão, rachaduras, etc. em uma construção soldada, independentemente de sua orientação.
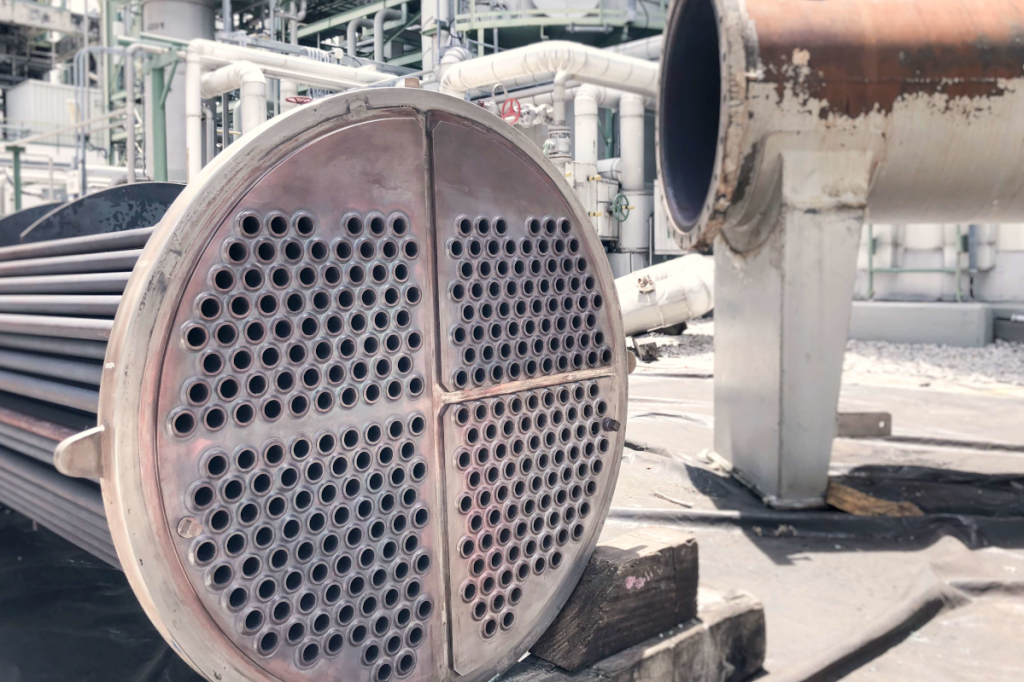
Métodos END para inspeção de trocadores de calor e tubulações de fornos
Para manter os tubos do trocador de calor em condições ideais, os testes não destrutivos regulares são cruciais para a detecção de falhas que podem levar a uma transferência de calor deficiente e ao aumento dos custos operacionais. A inspeção de rotina não só ajuda a evitar falhas repentinas, mas também pode ajudar a prolongar a vida útil de seus trocadores de calor tubulares.
Fornecemos os seguintes métodos de END para inspeção de trocadores de calor:
- Teste eletromagnético de campo remoto (RFET) - Eddy Current: Detectar rachaduras muito pequenas em materiais condutores.
- Sistema de inspeção rotativa interna (IRIS): Determina a espessura dos tubos inundando-os e inserindo um transdutor dentro do tubo.
- Inspeção em linha (ILI) com sensores ultrassônicos: Detecta a corrosão e a deformação da tubulação e da tubulação de processo enviando uma sonda especial (pig inteligente) para dentro da tubulação.
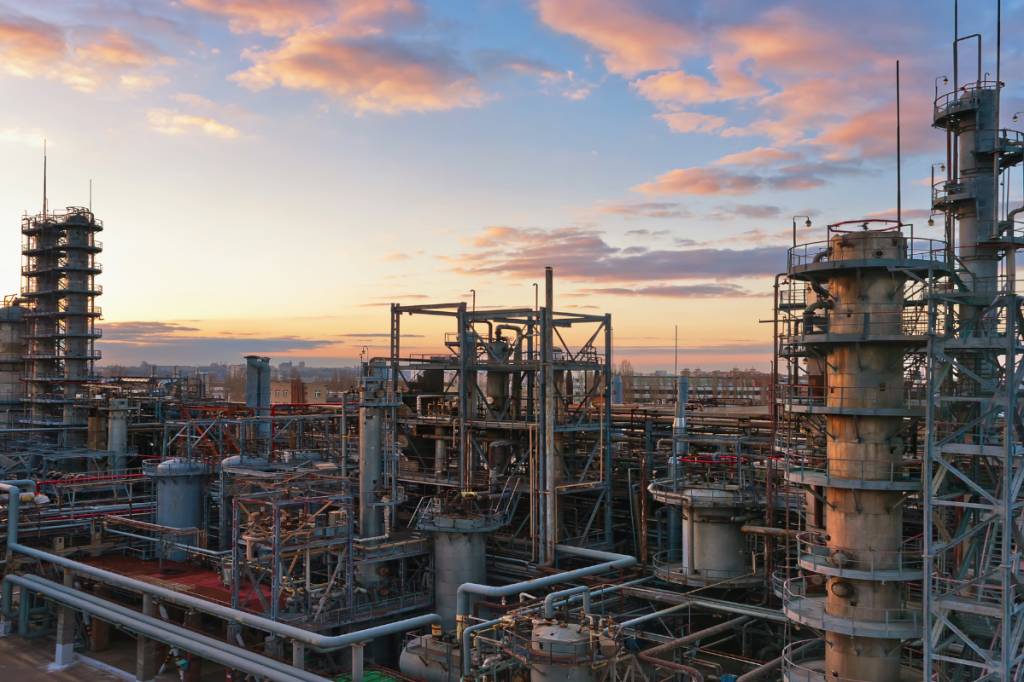
Métodos END para Inspeção de Ataque de Hidrogênio em Alta Temperatura
Devido à presença de hidrogênio, em combinação com alta temperatura e pressão, o fenômeno de um ataque de hidrogênio em alta temperatura (HTHA) pode ocorrer dentro de vasos e tubulações, tornando as plantas e os sistemas suscetíveis a danos.
Uma vez estabelecido o risco da presença de HTHA, é fundamental inspecionar o equipamento para verificar se há sinais de HTHA. No estágio inicial do desenvolvimento da HTHA, pode ser difícil prever sua progressão. Se o dano suspeito já estiver presente, a velocidade de progressão pode se acelerar, por exemplo, devido a mudanças no processo. Portanto, é sempre desejável detectar a HTHA o mais cedo possível e monitorar seu desenvolvimento com mais frequência.
É muito difícil detectar danos por HTHA nos estágios iniciais de seu desenvolvimento. A recomendação mais recente do setor é usar uma combinação de técnicas avançadas de ensaios não destrutivos (END):
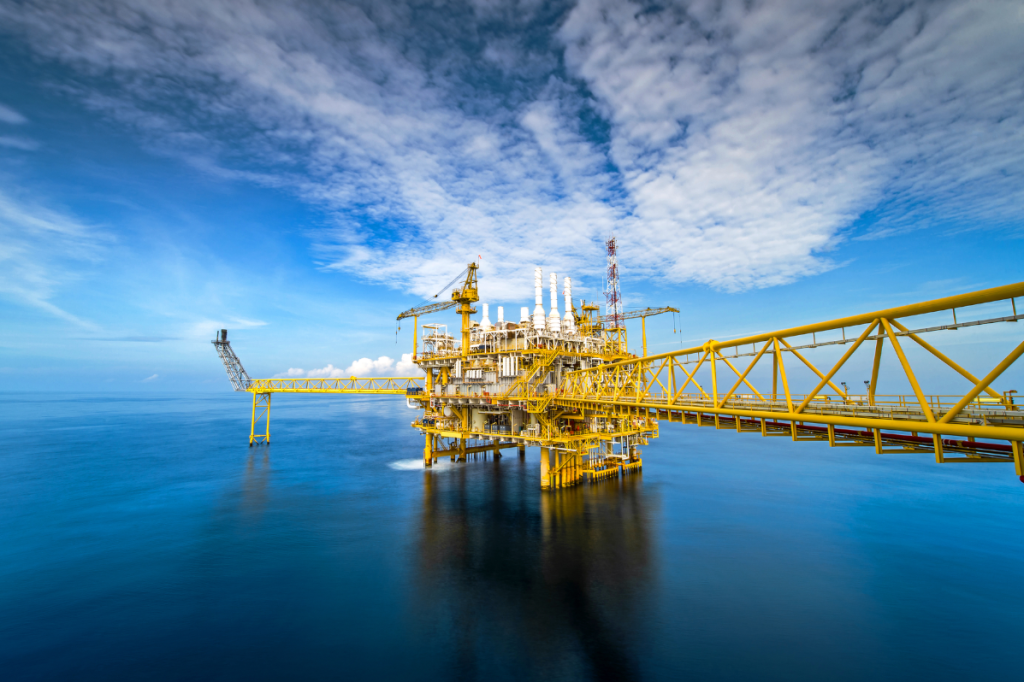
Métodos END para registro de perda de material (inspeção de poços offshore)
Ao avaliar a condição dos invólucros e condutores de poços offshore usando ensaios não destrutivos, é necessário caracterizar com precisão a corrosão oculta, identificando as camadas afetadas e medindo a quantidade de perda de metal e o pillowing associado devido ao processo de corrosão. A TÜV Rheinland desenvolveu um método de inspeção exclusivo para o setor offshore:
Otimização da inspeção: Aumente a confiabilidade de sua fábrica otimizando suas inspeções
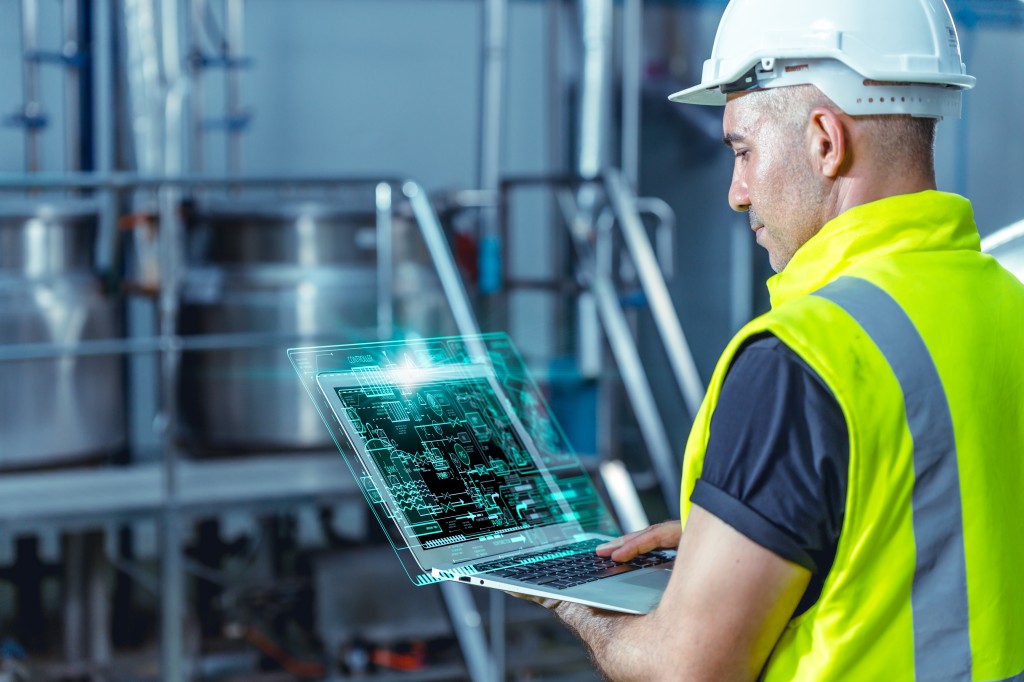
A TÜV Rheinland oferece serviços de otimização para inspeções com o objetivo de aumentar a confiabilidade e a eficiência da planta, resultando na redução do tempo de inatividade e das paradas não planejadas.
Soluções sob medida, como inspeções não intrusivas (NII), inspeções baseadas em risco (RBI) e programas de Vida Útil Estendida / Adequação ao Serviço, visam mecanismos de danos específicos e reduzem os custos de manutenção.
O foco está no uso de técnicas avançadas para manter e garantir a integridade da planta durante a operação. Com uma rede global de especialistas, a TÜV Rheinland desenvolve estratégias personalizadas para melhorar a segurança operacional e a viabilidade de suas plantas industriais.
Contact
