Reduzir o escopo e a frequência das paradas e mitigar os riscos de paradas não planejadas e acidentes
A produção contínua e ininterrupta pode ser alcançada com o uso de soluções especializadas de inspeção não intrusiva (NII) no fluxo. Isso significa que os operadores de ativos não precisam fechar suas instalações para inspecionar as propriedades do material de equipamentos críticos.
Especialmente no setor petroquímico, de processos, de gás e de energia convencional, é necessária a avaliação periódica dos ativos industriais. Equipamentos críticos (como tubulações de transporte e equipamentos de pressão) podem ser perigosos devido à possibilidade de queima ou explosão, com riscos subsequentes para as pessoas e o meio ambiente. Com o aumento da idade dos ativos industriais e dos sistemas de pressão, eles podem se deteriorar mais rapidamente devido à corrosão e às reações do processo. Podem ocorrer grandes defeitos, o que pode causar paradas não planejadas com longos períodos de inatividade da planta e levar a graves riscos à segurança, à saúde e ao meio ambiente. Para evitar esses riscos, recomenda-se a inspeção frequente de equipamentos críticos.
Desafio: Encontrar e avaliar defeitos no fluxo
A avaliação de danos de serviço não está definida nos códigos e padrões de NDT. No entanto, nossos especialistas em END podem fornecer os métodos de inspeção corretos com base no seu caso de uso individual, de modo que as descontinuidades e os defeitos em serviço nos componentes possam ser detectados em um estágio inicial e sem interrupção desnecessária das suas atividades de produção. A detecção precisa de falhas permite que você repare ou substitua materiais defeituosos antes que ocorram danos maiores.
Superar desafios específicos durante a operação contínua da planta
Como proprietário ou operador de ativos, você enfrenta desafios específicos e importantes ao tentar minimizar as interrupções e paradas de sua produção contínua:
- Riscos não controlados: Paralizações não planejadas podem ser o resultado de riscos não controlados ou mal gerenciados (por exemplo, acidentes como vazamento de óleo, risco de explosão).
- Riscos de segurança ao trabalhar em instalações operacionais: Há riscos a serem considerados ao inspecionar as instalações em operação. Inspetores, operadores e outras pessoas envolvidas estão expostos a riscos de segurança ao trabalhar em instalações em operação.
- Poluição ambiental e sustentabilidade: Além dos riscos à segurança, as atividades de remoção de produtos e limpeza das fábricas consomem muito tempo e podem levar a um alto nível de poluição ambiental, como contaminação por óleo e resíduos químicos.
- Paralisações não planejadas com longos períodos de inatividade: As paradas não planejadas causadas por defeitos não detectados geram altos custos devido à perda de tempo de produção e aos reparos de emergência. No caso de uma parada não planejada, o proprietário do ativo precisa primeiro estabelecer a causa do defeito para corrigi-lo, o que pode ser um processo demorado. A quebra de equipamentos críticos com prazos de entrega longos pode fazer com que a fábrica fique inoperante por um longo período.
- Preparação para paralisações e reparos planejados: Em contraste com as paradas não planejadas, os operadores de ativos também podem interromper a produção propositalmente para realizar inspeções em serviço. O gerenciamento das atividades de parada é muito mais difícil sem um planejamento detalhado baseado em informações precisas antes da parada. Sem os dados de inspeção mais recentes, é difícil ter uma avaliação precisa do escopo da inspeção e da manutenção e, consequentemente, a duração das paradas planejadas pode demorar muito mais. Para equipamentos em que são esperados reparos, as inspeções não intrusivas (NII) no fluxo permitem que a inspeção seja realizada antes da parada da fábrica para confirmar o escopo dos reparos e da manutenção necessários.
- Plantas envelhecidas e muito usadas são mais propensas a defeitos: Especialmente os componentes que são expostos a condições extremas (por exemplo, trabalho de soldagem, tratamento térmico ou condições climáticas) têm maior probabilidade de desenvolver falhas. Sem inspeções periódicas avançadas de ensaios não destrutiveis, o proprietário do ativo não pode avaliar com precisão a condição dos componentes e evitar paradas não planejadas. A inspeção completa do equipamento crítico também é necessária para realizar uma avaliação precisa do tempo de vida útil (LTA).
- Atividades mecânicas: As atividades mecânicas, como soldagem e tratamento térmico, podem criar riscos e problemas adicionais para os vasos e equipamentos de pressão.
- Capacidade total de produção: É necessário conhecer a condição atualizada da planta para decidir até que ponto a capacidade total de produção pode ser utilizada. Somente quando o proprietário do ativo conhece as condições da instalação, a produção pode ser aumentada sem prejuízo da segurança.
Nós o ajudamos a reduzir o escopo das paradas programadas e a minimizar os riscos de HSE, especialmente durante a extensão da vida útil de seus equipamentos críticos. Oferecemos um amplo portfólio de métodos avançados de END não intrusivos no fluxo para superar esses principais desafios e atingir suas metas individuais.
Nossos métodos avançados de Ensaios Não Destrutivos: Aumente a confiabilidade do seu equipamento com nossas inspeções precisas no fluxo
Dependendo da degradação esperada, da geometria, da espessura e do tipo de material, oferecemos métodos avançados de END adaptados às suas necessidades. Dê uma olhada nas diferentes aplicações e em nossa linha completa de técnicas de Inspeção Não Intrusiva:
/tuv-rheinland-corrosion-mapping_core_1_x.jpg)
Métodos END para detecção de corrosão no fluxo
A corrosão pode estar presente em muitas formas diferentes, como afinamento geral da parede, ou um pequeno ataque local, como pitting, ou um ataque semelhante a uma rachadura nos limites dos grãos, ou Corrosão sob isolamento. O conhecimento do padrão de dano esperado é importante para a seleção da técnica a ser aplicada. A redução geral do desbaste requer outros métodos além do ataque preferencial de soldas.
As técnicas abaixo podem ser usadas no fluxo para detectar a corrosão e determinar sua extensão.
- Mapeamento de corrosão com SeeScan até 325 °C: Os resultados da medição de espessura são apresentados em um mapa topográfico colorido de fácil compreensão.
- Phased Array (PA) até 425 °C: Método de alta resolução para maior probabilidade de detecção.
- Tempo de Difração de Voo (ToFD) até 485 °C: Detecte e dimensione com precisão a corrosão para um monitoramento preciso.
- Teste Ultrassônico (UT) para verificação de pontos até 425 °C: Determine a espessura dos pontos normalmente usados quando se espera apenas corrosão geral.
- Teste Ultrassônico de Longo Alcance (LRUT) / Onda Guiada até 350 °C: Detecta corrosão e erosão sob o isolamento.
- Pulsed Eddy Current (PEC) até 300 °C: Avalia a condição de componentes de aço de baixo carbono penetrando através de camadas de isolamento e revestimento que não são magnéticas e não conduzem eletricidade (ou seja, sem remover o isolamento ou o revestimento).
- Teste Radiográfico (RT) Digital: Determina a espessura criando um perfil digital usando uma placa sensível à radiação para transferir os dados para um sistema de computador.
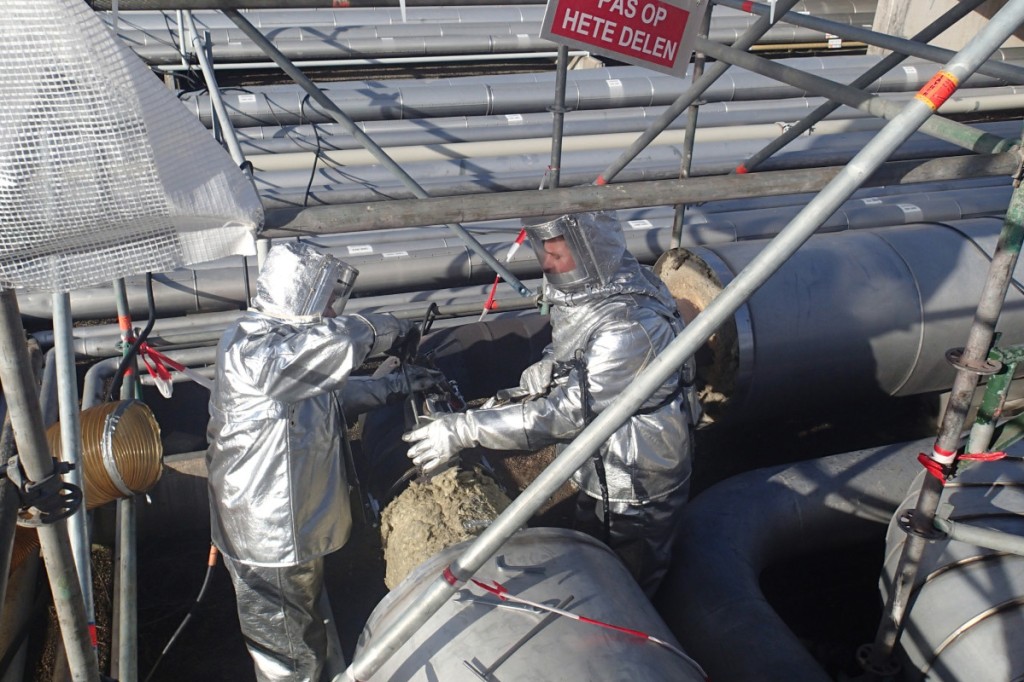
Métodos END para detecção local de rachaduras e vazamentos no fluxo
As rachaduras ou outros ataques locais podem levar a vazamentos ou até mesmo ao colapso. Se forem esperadas falhas semelhantes a rachaduras, o teste ultrassônico (UT) manual no fluxo, a difração de tempo de voo (ToFD) ou o Phased Array (PA) são as técnicas apropriadas a serem usadas. Ao contrário do exame ultrassônico de rotina das soldas de topo, as falhas em serviço são difíceis de detectar devido à complexidade da falha, à geometria difícil e, às vezes, ao acesso restrito às superfícies de inspeção.
O teste de emissão acústica fornece avisos antecipados e detecta rachaduras por corrosão ativa em um estágio inicial. Os sinais de vazamentos podem ser detectados mesmo quando as rachaduras ainda não foram notadas; no entanto, a geometria e o processo do equipamento podem influenciar significativamente os resultados.
Oferecemos os seguintes métodos para detectar possíveis rachaduras de material no fluxo:
- Teste Manual Ultrassônico (UT) até 425 °C: O método mais convencional para defeitos facilmente detectáveis.
- Exame de solda com Phased Array (PA) de até 425 °C: Detecte pequenas falhas, identifique e monitore a degradação potencialmente prejudicial.
- Exame de solda por difração de tempo de voo (TOFD) até 485 °C: Detecte e dimensione com precisão falhas e rachaduras para fins de monitoramento.
- Teste de emissão acústica de até 400 °C: Detecte deformações metálicas crescentes, rachaduras, defeitos e corrosão ativa em um estágio inicial.
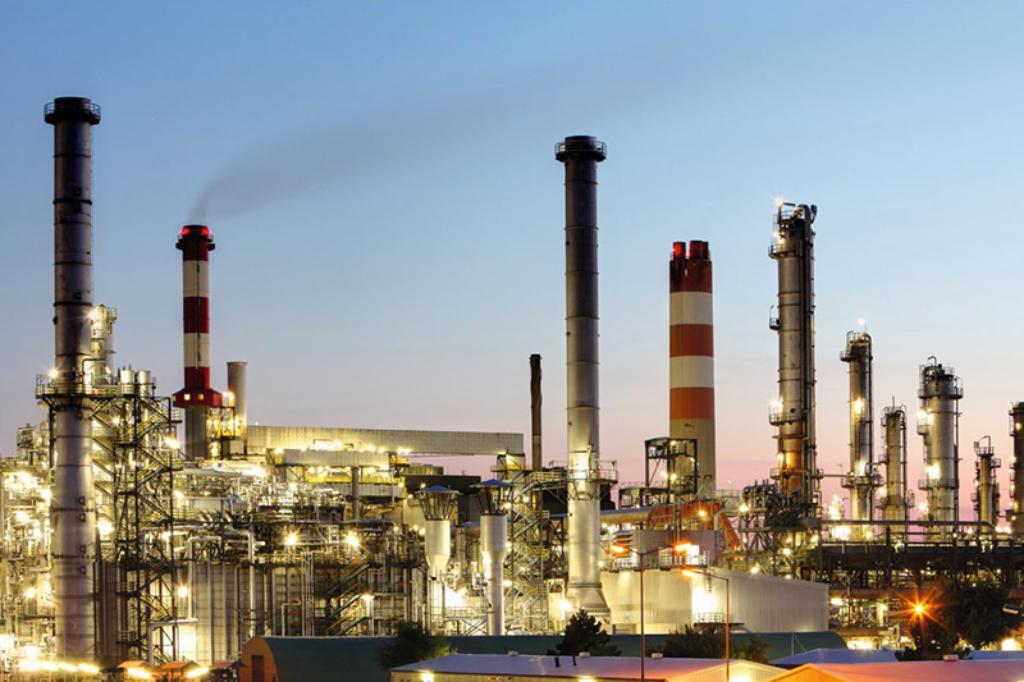
Monitoramento remoto de condições
Ao coletar e avaliar os dados relevantes e atualizados de integridade mecânica, o status de todo o equipamento ou de um único componente pode ser monitorado continuamente e uma declaração sobre sua capacidade funcional pode ser feita. Nossos especialistas aplicam as mais recentes tecnologias de sensores para realizar o monitoramento remoto contínuo das condições dos ativos industriais
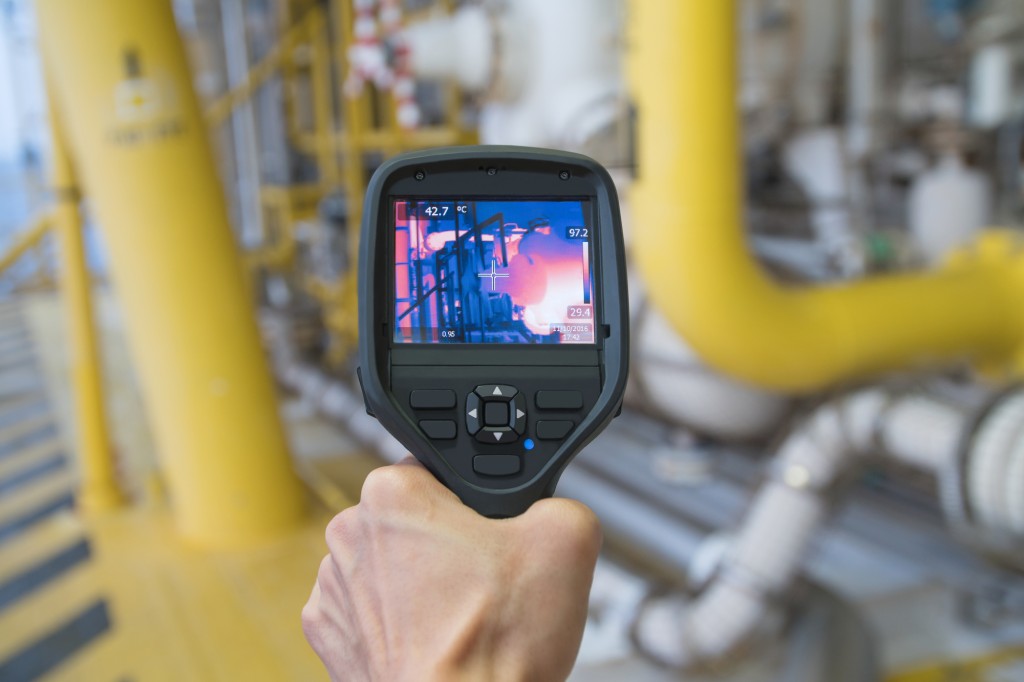
Métodos de END para distribuição de calor
A distribuição de calor na superfície do componente pode ser observada com uma câmera infravermelha para detectar anomalias (por exemplo, pontos quentes, vazamento, afinamento da parede, bloqueio). Fornecemos o seguinte método ANDT:
- Inspeção termográfica distribuição de calor
Otimização da inspeção: Aumente a confiabilidade de sua fábrica otimizando suas inspeções
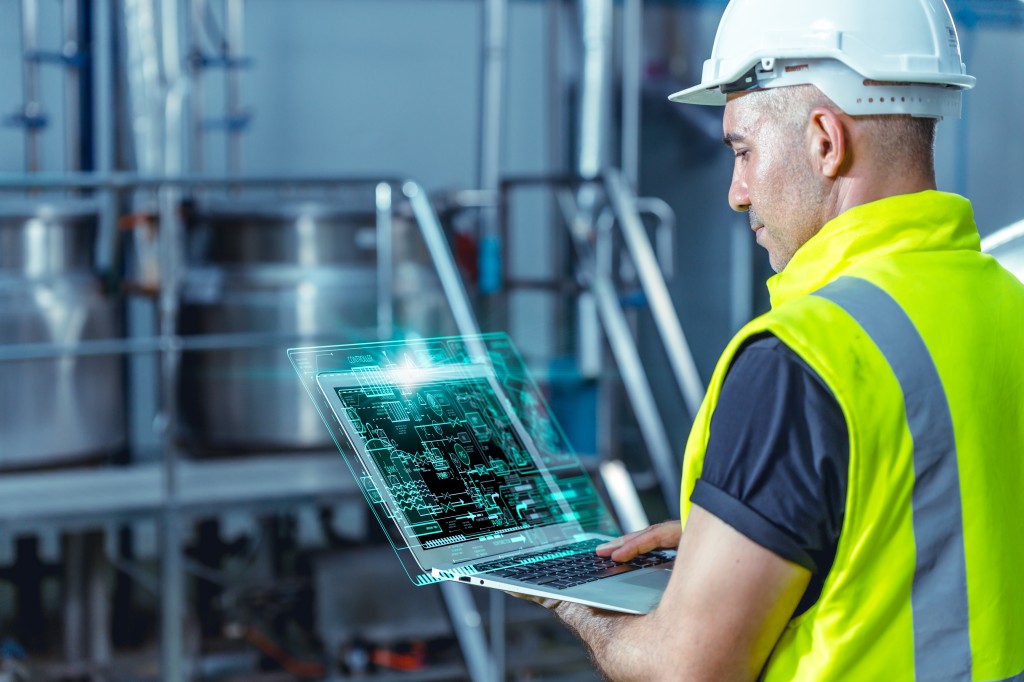
A TÜV Rheinland oferece serviços de otimização para inspeções com o objetivo de aumentar a confiabilidade e a eficiência da planta, resultando na redução do tempo de inatividade e das paradas não planejadas.
Soluções sob medida, como inspeções não intrusivas (NII), inspeções baseadas em risco (RBI) e programas de Vida Útil Estendida / Adequação ao Serviço, visam mecanismos de danos específicos e reduzem os custos de manutenção.
O foco está no uso de técnicas avançadas para manter e garantir a integridade da planta durante a operação. Com uma rede global de especialistas, a TÜV Rheinland desenvolve estratégias personalizadas para melhorar a segurança operacional e a viabilidade de suas plantas industriais.
Contato
