Environmental Simulation for Electrical Products
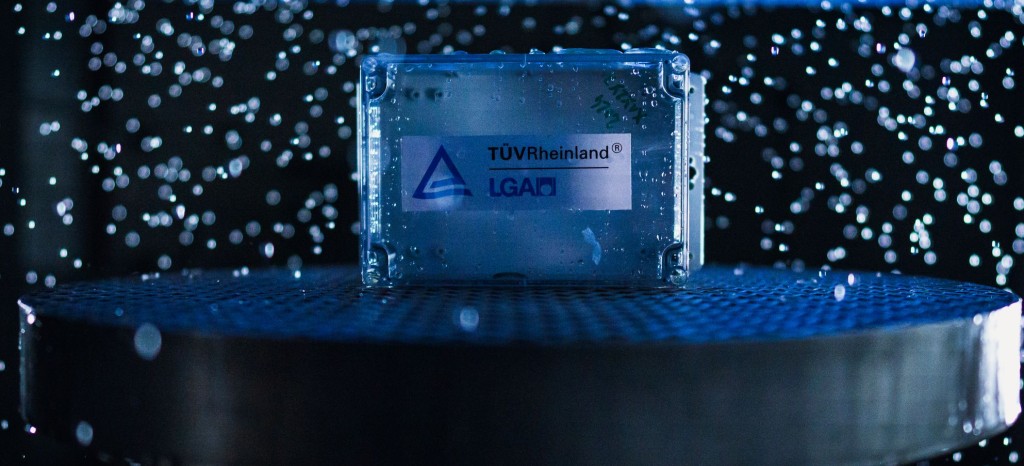
More Safety for Your Electrical Devices through Environmental Simulation
Electrical devices and their accessories may be exposed to massive climate change and mechanical stress. Variations in temperature, moisture, dust, shocks or strong vibrations should not, however, have an impact on the functionality of the devices. Are your electrical components or devices suitable for outdoor use?
TÜV Rheinland services in the field of quality assurance and control can help to ensure the safety of electrical devices. Similarly, the operational reliability of the electrical components is maintained through regular functional tests.
Our laboratory for environmental simulation offers climate tests for your electrical products according to all required standards. Whether IEC/EN 60068, ISO 16750, EN 61373, ISO 20653 or customer-specific requirements as VW80000 – we find the right standard for every product. Our test laboratory is accredited in accordance with DIN EN ISO/IEC 17025, so the test protocols and reports prepared by us are widely accepted.
Our core competence: component testing according to company guidelines for the automotive, rail, ship and aerospace supplier industries. With our impartial tests, you document the functional reliability of your electrical products in extreme situations.
Benefits at a Glance
With vibration and climate tests by the independent experts at TUV Rheinland you
- Minimize your liability risk and protect yourself against claims for damages.
- Can take advantage of generally accepted testing protocols for targeted marketing.
- Strengthen the confidence in the quality and safety of your products.
- Offer your customers an important decision-making aid in their product selection.
- Will gain confidence in the durability of your products through extensive testing, certified by an impartial testing institution.
Our experts welcome your questions and are available for further information on environmental simulations.
Our Environmental Simulation Services
To ensure the safety of your electrical products, we offer the following services in our laboratory:
- HALT (High Accelerated Life Test) and HASS (High Accelerated Stress Screening) testing
- Climate and temperature tests (cold, dry and moist heat from -70 °C to +180 °C)
- Corrosion tests
- Vibration tests with temperature conditions (sine, random noise, combined sine and random noise, resonance investigations)
- Shock tests
- Transport tests (drop test, vibration, shock test)
- IP code tests (IP10–IP69K)
- Splash proof tests and ice water tests
- Harmful gas, single or mixed gas tests
- Complete qualification tests on plugs and plug connections
Safety for Your Electrical Products
Numerous vibration and climate tests are verified in our lab for environmental simulation, ensuring the safety of your electrical products and their accessories. We support you in testing of compliance to all the necessary legal requirements. Environmental simulation tests can help detect potential problems in the electrical components of your products.
Electrical Testing Services
Take a look at our laboratory in Nuremberg, Germany. Watch the video now!
Testing of electromobility components
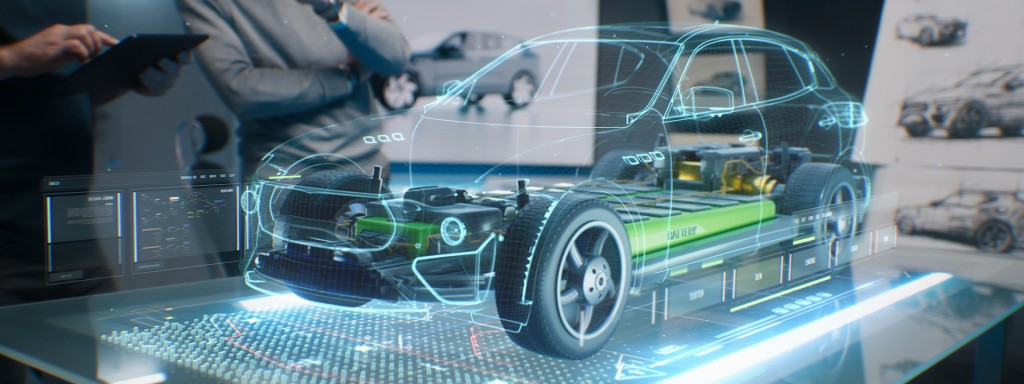
Mobility is our passion. This is especially true today, as mobility is being reinvented. That is why we love to put our expertise and experience at the service of innovative companies that are helping to shape electromobility. Discover our services for your components from powertrain to charging technology. Learn more!
Thermal / Environmental Tests
The Cold Test:
Purpose of this test: The main objective of the cold test is to determine the ability of the components, equipments or other articles to be used to be transported or stored at low temperatures.
Test Procedure: The specimen is introduced into the chamber which is at the same temperature as that of the laboratory. The temperature is then adjusted to a temperature appropriate to the degree of severity (as specified in the relevant specification). After temperature stability of the test specimen has been reached, the specimen is exposed to these conditions for the specified duration. This test is performed with reference to IEC / EN 60068-2-1: 2007 or Product family standard for more details. This can be performed from an ambient temperature for upto -70 °C.
Dry Heat Test:
Purpose of this test: This test is performed to determine the ability of the components, equipments or other articles to be used, to be transported or stored at a high temperature.
Test Procedure: The specimen is introduced into the chamber, which is at the same temperature as that of the laboratory. The specimen shall then be switched on or electrically loaded and checked to ascertain whether it is capable of functioning in accordance with the relevant specification. The specimen shall remain in the operating condition in accordance with the duty cycle and at the loading condition (if applicable) as prescribed by the relevant specification. This test will be performed with reference to IEC / EN 60068-2-2:2007 or Product family standard for more details. This can be performed from an ambient temperature for upto +200 °C.
Damp Heat(Steady State Humidity/ Cyclic Humidity) Test:
Purpose of this test: The Damp Heat test is performed to determine the suitability of components, equipment or other articles for use, for transportation and storage under the conditions of high humidity – combined with cyclic / steady state temperature and in general temperatures producing condensation on the surface of the specimen. If the test is being used to verify the performance of a specimen whilst it is being transported or stored in packaging, then the packaging will normally be fitted when the test conditions are being applied.
Test Procedure: The specimen is introduced into the chamber and the temperature of the chamber shall be raised to the appropriate upper temperature prescribed by the relevant specification. After the prescribed time duration, the temperature shall then be maintained as per the standard. This test will be performed with reference to BS EN / IEC 60068-2-30:2005 for damp heat, cyclic humidity test, BS EN / IEC 60068-2-38:2009 Composite temperature/humidity cyclic test and IEC 60068-2-78:2001 for damp heat, steady state humidity test or Product family standard for more details. This can be performed from 10% to 98 % rh at various temperatures.
Thermal (Shock) Cyclic Test:
Purpose of this test: The purpose of this test is to ensure that the product will survive during fluctuating environmental (temperature) conditions. Rapid changes of temperature may be expected when the equipment is transported from warm indoor environments into cold open air conditions or vice versa or when the equipment is suddenly cooled by rainfall or by immersion in cold water, in externally mounted airborne equipment and under certain conditions of transportation and storage. The components will undergo stress due to the changing temperature when high temperature gradients build up in the equipment after it is switched on.
Test Procedure: The test specimen shall be exposed to the cold temperature TA. TA shall be maintained for the specified period t1, (t1 including an initial time not longer than 0.1 and t1 for temperature stabilization of the air temperature in the chamber).The specimen shall then be exposed to a hot temperature TB, in a period t2, which should not be more than 3 min. t2 shall include the time needed for the removal from one chamber and the insertion into the second chamber as well as any dwelling time at the ambient temperature of the laboratory. This test will be performed with reference to IEC / EN 60068-2-14, etc, or product family standard for more details. The test can be performed at -70 °C to 190 °C.
Salt Fog/Salt Mist/Combined Salt/ Humidity Cyclic Test:
Purpose of this test: The salt fog test is a standardized test method used to check corrosion resistance of the coated samples. Coatings provide corrosion resistance to the metallic parts made of any kind of steel or brass. Since coatings can provide a high corrosion resistance through the intended life of the part in use, it is necessary to check the corrosion resistance of the metal parts.
Test Procedure: This practice provides a controlled corrosive environment which has been utilized to produce relative corrosion resistance information for specimens of metals and coated metals exposed in a given test chamber. The prediction of performance in natural environments has seldom been correlated with salt spray results when used as stand-alone data. The test consists of spraying salt solution and storing the products in the damp chamber. After each storage period, functional tests are to be performed. This test will be performed at temperatures of upto 35 °C with 100% rh with reference to IEC / BS EN 60068-2-11:2007, IEC / EN 60068-2-52, IS 9000: part 11:1983 and ASTM B 117-07 or product family standard for more details.
Ingress Protection Test
Purpose of this test: This test is performed to verify the degree of protection provided by enclosures of electrical equipments as regards:
- Protection of persons against access to hazardous parts inside the enclosure
- Protection of the equipment inside the enclosure against ingress of solid foreign objects
- Protection of the equipment inside the enclosure against harmful effects due to the ingress of water.
Degree of protection against access to hazardous parts indicated by the first characteristic numeral
- IP0x – No protection against contact and ingress of objects
- IP1x – Protected against access to hazardous parts with the back of the hand (The access probe, sphere of 50mm, shall have adequate clearance from hazardous parts)
- IP2x – Protected against access to hazardous parts with a finger (The jointed test finger of 12 mm, 80 mm length, shall have adequate clearance from hazardous parts)
- IP3x – Protected against access to hazardous parts with a tool (The access probe of 2.5mm shall not penetrate)
- IP4x – Protected against access to hazardous parts with a wire (The access probe of 1.0 mm shall not penetrate)
- IP5x – Protected against access to hazardous parts with a wire (The access probe of 1.0 mm shall not penetrate)
- IP6x – Protected against access to hazardous parts with a wire (The access probe of 1.0 mm shall not penetrate)
Degree of protection against access by solid foreign objects indicated by the first characteristic numeral
- IP0x – No protection against contact and ingress of objects
- IP1x – Protected against solid foreign objects of 50 mm and more. (The object probe, sphere of 50 mm, shall not fully penetrate)
- IP2x – Protected against solid foreign objects of 12.5 mm and more (The object probe, sphere of 12.5 mm, shall not fully penetrate)
- IP3x – Protected against solid foreign objects of 2.5 mm and more (The object probe, sphere of 2.5 mm, shall not penetrate at all)
- IP4x – Protected against solid foreign objects of 1.0 mm and more (The object probe of 1.0 mm, shall not penetrate at all)
- IP5x – Dust Protected (Ingress of dust is not totally prevented, but dust shall not penetrate in such a quantity as to interfere with the satisfactory operation of the apparatus or to impair safety)
- IP6x – Dust-tight (No ingress of dust)
Degree of protection against water indicated by the second characteristic numeral
- IPx0 – No protection against contact and ingress of water drop
- IPx1 – Protected against vertically falling water drops (vertically falling drops shall have no harmful effects)
- IPx2 – Protected against vertically falling water drops when the enclosure is tilted up to 15° (vertically falling drops shall have no harmful effects when the enclosure is tilted at any angle up to 15° on either side of the vertical)
- IPx3 – Protected against spraying water (water sprayed at an angle up to 90° on either side of the vertical shall have no harmful effects)
- IPx4 – Protected against splashing water (water splashed against the enclosure from any direction shall have no harmful effects)
- IPx5 – Protected against water jets (water projected in jets against the enclosure from any direction shall have no harmful effects)
- IPx6 – Protected against powerful water jets (water projected in powerful jets against the enclosure from any direction shall have no harmful effects)
- IPx7 – Protected against the effects of temporary immersion in water (Ingress of water in quantities causing harmful effects shall not be possible when the enclosure is temporarily immersed in water under standardized conditions of pressure and time)
- IPx8 – Protected against the effects of continuous immersion in water (Ingress of water in quantities causing harmful effects shall not be possible when the enclosure is continuously immersed in water under conditions which shall be agreed on between the manufacturer and user but which are more severe than numeral 7)
Test Procedure: During the test the water temperature should not differ by more than 5°C from the temperature of the specimen under test. If the water temperature is more than 5°C below the temperature of the specimen, a pressure balance shall be provided for the enclosure. During the test, the moisture contained inside the enclosure may partly condense. The dew which may thus deposit itself shall not be mistaken for ingress of water. For the purpose of the test, the surface area of the enclosure is calculated with a tolerance of 10 %. This test will be performed with reference to IEC / EN 60529-1 or product family standard for more details.
Mechanical Stability Tests
Vibration and Shock Testing:
Purpose of this test: This test demonstrates the adequacy of specimens to resist dynamic loads without unacceptable degradation of its functional and/or structural integrity when subjected to the specified, random, vibration test requirements. This test is for specimens that may be subjected to vibrations of a stochastic nature resulting from transportation or operational environments, for example in aircraft, in space vehicles and land vehicles. It is primarily intended for unpackaged specimens and for items in their transportation container when the latter may be considered a specimen by itself.
Test Procedure: The specimen shall be excited in each of the preferred testing axes in turn (unless otherwise prescribed by the relevant specification). If the specimen is sensitive to gravity, for example a mercury tilt switch, then vibrations may only be applied in its normal service position and shall be prescribed by the relevant specification. This test will be performed with reference to IEC /BS EN 60068-2-64:2008 or product family standard for more details. This test can be performed from 5 Hz to 2500 Hz.
Impact Hammer Test:
Purpose of this test: The Impact Hammer test is performed to determine the ability of a specimen to withstand specified severities of impact. It is used in particular to demonstrate an acceptable level of robustness when assessing the safety of a product and is primarily intended for the testing of electro-technical items.
Test Procedure: The specimens are mounted on the plywood as in normal service. Where it is not possible to mount the specimen directly onto the plywood, a suitable adapter would need to be prescribed by the relevant specification. It consists of the application to the specimen of a prescribed number of impacts defined by their impact energy and applied in the prescribed directions. This test will be performed with reference to IEC /BS EN 60068-2- 75:1997 or product family standard for more details.
Free Fall Test:
Purpose of this test: The purpose of this test is to simulate (in equipment-type specimens primarily), the effects of knocks and jolts which may be received during the rough handling of equipment on a work bench or table or in operational use.
Test Procedure: The specimen standing in its normal position of use on a smooth, hard, rigid surface of concrete or steel is tilted about one bottom edge so that the distance between the opposite edge and the test surface is 25mm, 50mm or 100mm, as prescribed by the relevant specification, or so that the angle made by the test surface is 30°, whichever is less severe. It is then allowed to fall freely on to the test surface. The specimen shall be subjected to one drop about each of the four bottom edges. This test will be performed with reference to IEC /BS EN 60068-2-31:2008 or Product family standard for more details.
Key Pad Endurance Test:
Purpose of this test: As mobile phones are getting smaller, the keypads used for dialing numbers and typing text messages are also becoming smaller. These phones are subject to lot of daily use. So it is important to test these keypads to ensure their reliability.
Test Procedure: A basic system for keypad testing comprises a pneumatic keypad test fixture, equipped with a low capacity load cell. During the test, the load profile and sometimes the displacement characteristic of the key press are monitored.
Flame Tests
Glow Wire Test:
Purpose of this test: The Glow Wire test is carried out to ensure that, under defined conditions, the glow-wire does not cause ignition of parts, and that a part, if ignited, has a limited duration of burning without spreading fire by flames or by burning or glowing particles falling from the test specimen.
Test Procedure: The test specimen shall be so arranged that the tip of the glow-wire is applied to the part of the surface of the test specimen which is likely to be subjected to thermal stresses in normal use. The glow-wire shall be maintained as close to the horizontal as is practicable. This test will be performed with reference to IEC / EN 60695-2-11 or Product family standard for more details. This test can be performed upto the temperature of 800 °C.
Needle Flame Test:
Purpose of this test: This test is performed to determine that under defined conditions, the test flame does not cause ignition of parts, or that a combustible part ignited by the test flame has a limited duration of burning or a limited extent of burning, without spreading fire by flames or burning or glowing particles falling from the test specimen.
Test Procedure: The test flame is applied to that part of the surface of the test specimen which is most likely to be affected by flames resulting from normal use or from faulty conditions. The duration of application of the test flame shall be as specified in the relevant specification .This test will be performed with reference to IEC / EN 60695-11-5, IEC / EN 60335 – 1 is for household and similar electric appliances, IEC / EN 60950 – 1 is for information technology equipments, IEC / EN 61010 – 1 is for measurement, control and laboratory equipments, IEC / EN 60065 is for audio, video and similar electronic apparatus or product family standard for more details.
Tracking Index Test:
Purpose of this test: The Tracking Index test is performed to determine the proof and comparative tracking indices of solid insulating materials on pieces taken from parts of equipment and on plaques of material using alternating voltages. The proof tracking index is used as an acceptance criteria as well as a means for the quality control of materials and fabricated parts. The comparative index is mainly used for the basic characterization and comparison of the properties of materials.
Test Procedure: The upper surface of the test specimen is supported in an approximately horizontal plane and subjected to an electrical stress via two electrodes. The surface between the electrodes is subjected to a succession of drops of electrolyte either until the over-current device operates or until a persistent flame occurs or until the test period has elapsed. This test will be performed with reference to IEC / EN 60112 or product family standard for more details.
Flammability Test:
Purpose of this test: Flammability test determines the linear burning rate and the time of after-flame/afterglow as well as the damaged length of specimens. This is applicable to solid and cellular materials that have an apparent density of not less than 250 kg/m3 and is intended to serve as a preliminary indication of the behavior of these materials when exposed to a flame ignition source. The results make it possible to check the constancy of the characteristics of a material and provide an indication of the progress in the development of materials and a relative comparison and classification of various materials.
Test Procedure: A rectangular bar-shaped test specimen is supported horizontally or vertically by one end and the free end is exposed to a specified test flame. The burning behavior of the horizontally supported bar is assessed by measuring the linear burning rate. The burning behavior of the vertically supported bar is assessed by measuring the time of after-flame and afterglow and the extent of burning and dripping of flaming particles .This test will be performed with reference to IEC / EN 60512-11-10 , IEC / EN 60707 and ISO 9773 or product family standard for more details.
Contact
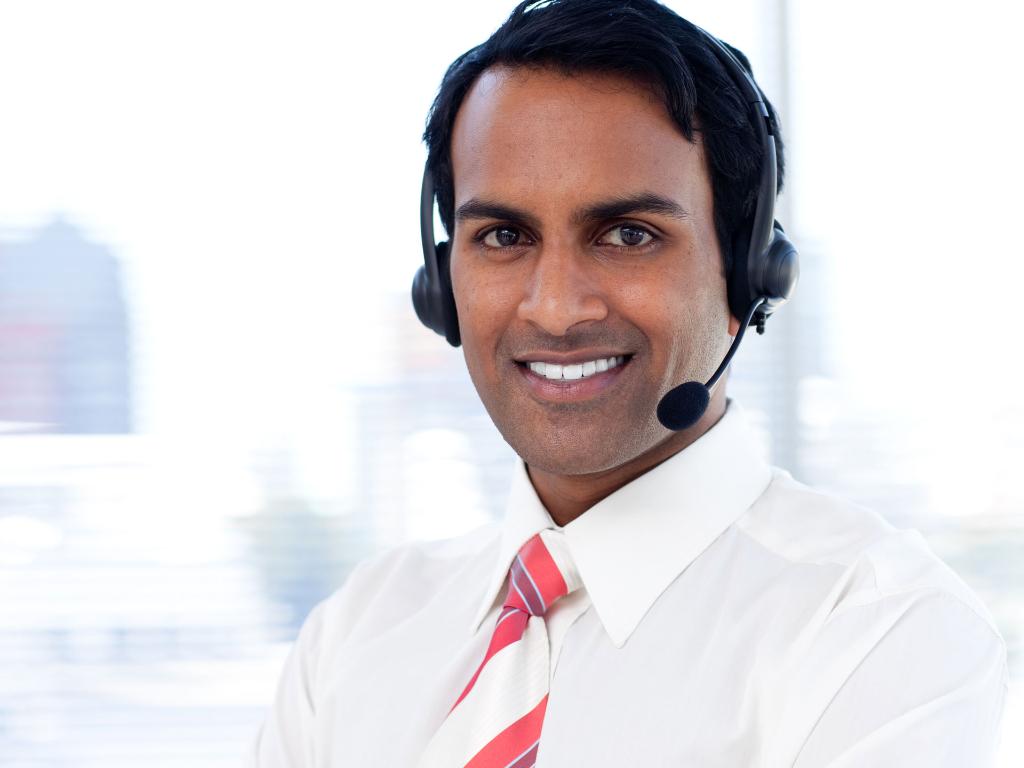