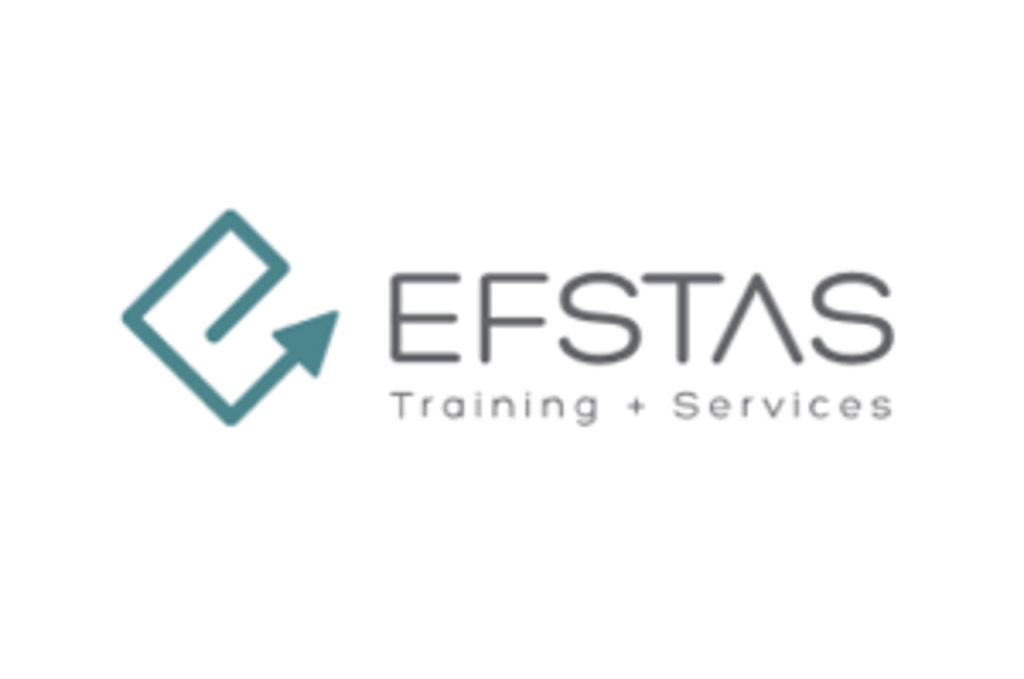
EFSTAS is an accepted course provider for the training “Functional Safety of Machinery” of the TÜV Rheinland Functional Safety Training Program.
The FS Engineer (TÜV Rheinland) certificate demonstrates competency in the fundamentals of Functional Safety and provides a skill set that is transferable from one work situation to another. It enables staff to fulfill responsibilities and to perform activities to recognised standards of competence on a regular basis, in order to
- reduce risks
- satisfy legal and regulatory requirements
- meet the organisation’s business objectives
- enable the organisation to meet contractual commitments.
By understanding:
- The principles and concepts of the internationally agreed safety related control system machinery standards IEC 62061, ISO 13849 including ISO 12100 and associated type A, B and C standards
- Risk Analysis methods for the determination of necessary measures for the reduction of risks at machines.
- The requirements of ISO 13849, application areas, restrictions regarding the applicability, software and documentation requirements, use of standard components in safety functions, proof of safety, verification and validation of safety functions. Examples for proof of FS according to ISO 13849-1.
- The requirements of IEC 62061, application areas, lifecycle model and documentation requirements, terminology used in the standard, requirements regarding safety relevant application software, proof of safety, verification and validation of safety functions. Examples for proof of FS according to IEC 62061.
- The selection and application of safety devices, their advantages and disadvantages, installation requirements and configuration requirements.
- Safety functions of Machines, Start/re-start interlock, start functions, Emergency off, emergency switching off, stop categories muting and their realization according to the different safety categories.
- Circuit and schematic requirements for connection of safety devices according to the different safety categories.
- The technical information required on components including extracting reliability data from manufacturers certificates, reports.
- SIL demonstration calculations such as average probability of dangerous failure per hour (PFH), safe failure fractions and hardware fault tolerance.
- How to identify and calculate the impact of common cause failures (Beta factor) on the reliability of protective systems
- Requirements for validation documentation to demonstrate that systems, (including application software and software and hardware integration) have been fully tested checked and approved.
Course Objectives
The course will equip participants with the knowledge for understanding and mastering the application, principles and requirements of the Functional safety of Machinery.
Successful participants, who also have sufficient functional safety experience, will achieve the prestigious FS Engineer (TÜV Rheinland) certificate in Machinery.
The course will provide three days of classroom tuition and practical guidance, mixed with practical exercises based on real life examples. Day four consists of a four-hour two-part proficiency examination with:
Part 1 = 70 multiple-choice questions
Part 2 = 12 open questions
Agenda
Who Should Attend?
Control & Instrument, Electrical, Process, Mechanical, Rotating Machinery and Safety Engineers as well as Operating and Maintenance personnel who are involved in any of the Machinery lifecycle phases for functional safety for machines from risk assessment, design through to installation, testing, maintenance and operation of machines.
Participant eligibility requirements
In accordance with the TÜV Functional Safety Training Program:
- A minimum of 3 years experience in the field of functional safety.
- University degree
- or equivalent engineering experience and responsibilities as certified by employer or engineering institution.