We support you with the continuous operation of your systems.
One of the tasks of plant operators, plant owners and maintenance managers is to ensure a smooth operation and, most importantly, avoid the risk of unplanned downtime or shutdowns. This requires an optimization of the processes relevant to operation and maintenance, which is achieved by continuous monitoring and inspections, by having skilled personnel for implementing standards, by substituting components, continuously developing new processes and taking measures to control safety and quality.
Our independent experts will support you to ensure the continuous operation of your systems, which will enable you to establish a competitive advantage for the future.
Key challenges within the design and concept phase:
Reducing complexity in the supply chain is crucial to avoiding bottlenecks and ensuring the availability of components. The integration of technologies such as predictive maintenance and data analysis offers new opportunities for accomplishing this, but it also poses challenges. Additionally, skilled personnel that is familiar with the regulatory requirements is needed.
The timely procurement and management of spare parts is critical to minimize downtimes. This requires an accurate inventory management and the ability to react to unforeseen demands. Additionally, some of the components used may be highly specialized and difficult to replace or maintain.
To ensure the continuity of operations and to minimize the risk of accidents or downtime, it is essential to comply with quality standards and safety regulations. A transparent documentation and communication are crucial in order to address liability issues at an early stage.
Supply chain services we offer to support you in this phase:
Secure your operations advantage
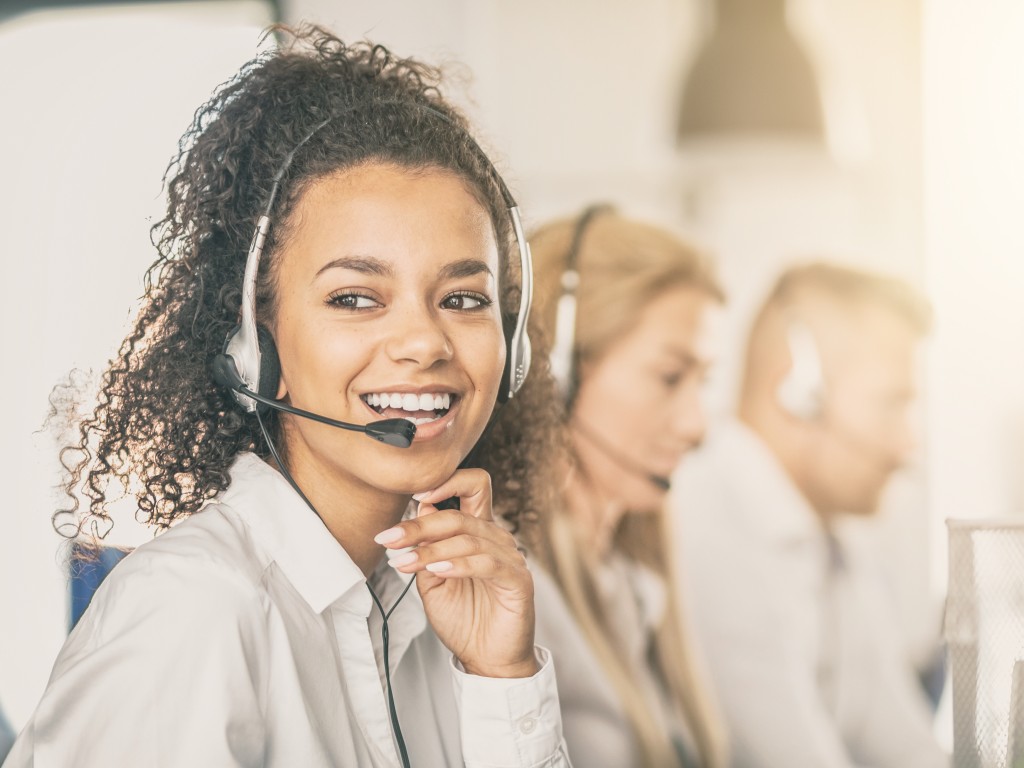