Reduce your fabrication costs with suitable (advanced) NDT solutions
Managing new construction especially in the oil and gas, (petro-)chemical and power industry, generally means major investment projects with many parties involved. Commonly for the large projects, the investors engage an EPC (engineering, procurement, construction) contractor to ensure the entire project runs smoothly. From the NDT perspective, the EPC contractor will guide the various pressure equipment manufacturers and constructors, who manufacture piping during both prefabrication and assembly. In addition to the timely availability of the various construction materials, all parties have a common interest: delivering the required quality at the lowest possible cost and on time.
For smaller projects, the EPC contractors are not necessarily involved, so the manufactures coordinate the construction of the industrial assets themselves. In this context, conventional and advanced NDT methods can be applied to check the quality of the new components. To perform these NDT inspections, the inspector has to follow defined requirements that are constantly changing.
Select the right NDT methods based on the design codes
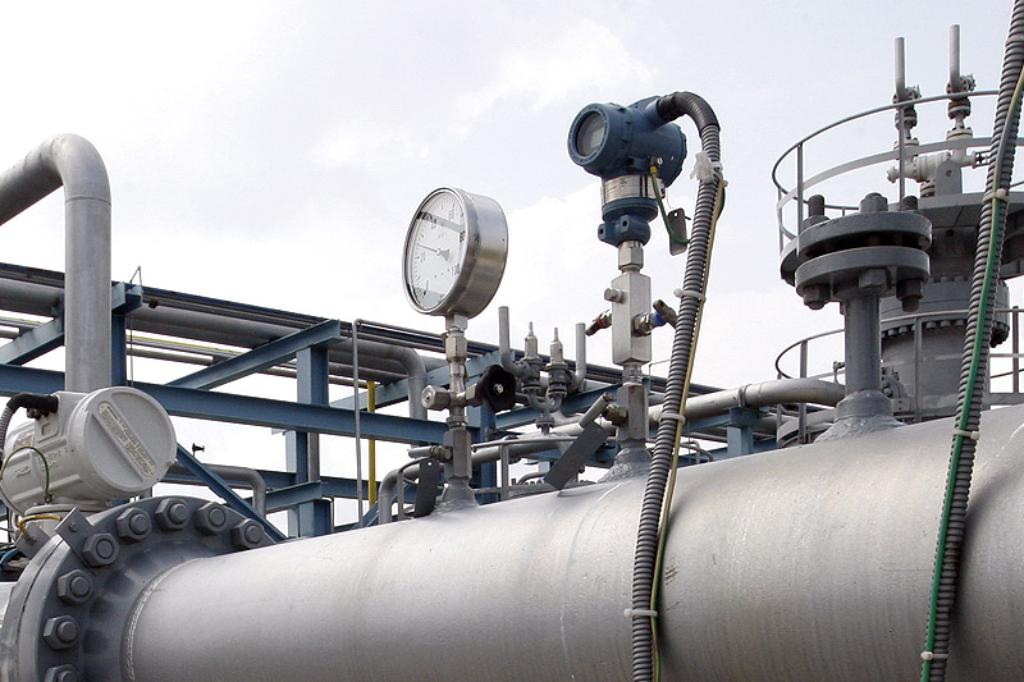
Quality acceptance criteria varies significantly from a project to project and from a client to client. In addition, the (advanced) NDT methods also differ significantly providing various options for assessment of quality criteria set by a client. Our certified NDT inspectors with decades of experience are familiar with the current requirements and the use of different NDT methods. That is why we can offer you a wide variety of NDT inspection techniques in accordance with relevant design specifications (e.g. ASME BPVC Code, ISO) or client specific requests.
Companies have to comply with the specific construction codes and standards, which also specify NDT inspection methods and the extent of examination. The right NDT method can be selected on a basis of different design codes for critical industrial assets like boilers and pressure vessels, which would fit best for your manufacturing process and goals.
Overcome your specific challenges with our NDT solutions
Considering the life cycle of a plant, special key challenges apply to its construction. EPC contractors and manufacturers have to overcome several hurdles:
Project lead times have a major impact on investments. EPC contractors and equipment manufacturers both benefit from reducing the construction time and costs. In this context, the selection of NDT methods depending on the design codes is crucial. In general, the conventional methods are used in new construction projects because they are considered to be cheaper. However, by selecting the right advanced NDT method, the fabrication time can be saved, resulting in a shorter lead time and therefore lower overall fabrication costs.
Major projects require highly skilled engineers at all levels. Availability of these engineers depends on several different factors such as region and investment budget. Also, the level of craftsmanship in some regions might not meet the level expected by global multinationals. Shortage of reliable skilled engineers may negatively impact on selection of suitable fabricators, quality control during the fabrication and overall expediting of the complex deliveries of equipment.
Manufacturing of a new industrial asset is complex due to constantly changing technical developments and environmental requirements. Based on newly sourced materials or changed regulations, it becomes more important to be up to date with the latest techniques available for quality control and assurance. Increasing demands for sustainable sourcing and manufacturing add further complexity to the managing your supply chain and choosing the best inspection strategy.
We can help you to overcome these key challenges during the manufacturing and construction phase. Our NDT experts advise you on your individual construction project and are able to apply a broad portfolio of conventional and advanced NDT methods in order to reduce your costs.
Overview of conventional and advanced NDT methods used during manufacturing of new plants and equipment
As a constructor or EPC contractor you might already know which NDT solutions you need to apply during manufacturing and construction of new plants. Here you find an overview of conventional and advanced NDT methods, which we can provide.
Our conventional NDT methods: Reliable well-known methods effectively covering majority of the challenges
We offer reliable and well-established NDT services tailored to the needs of EPC contractors and constructors, which prove conformity of the fabricated equipment to the required design specification. Our comprehensive non-destructive testing services include the full range of conventional methods for new constructions:
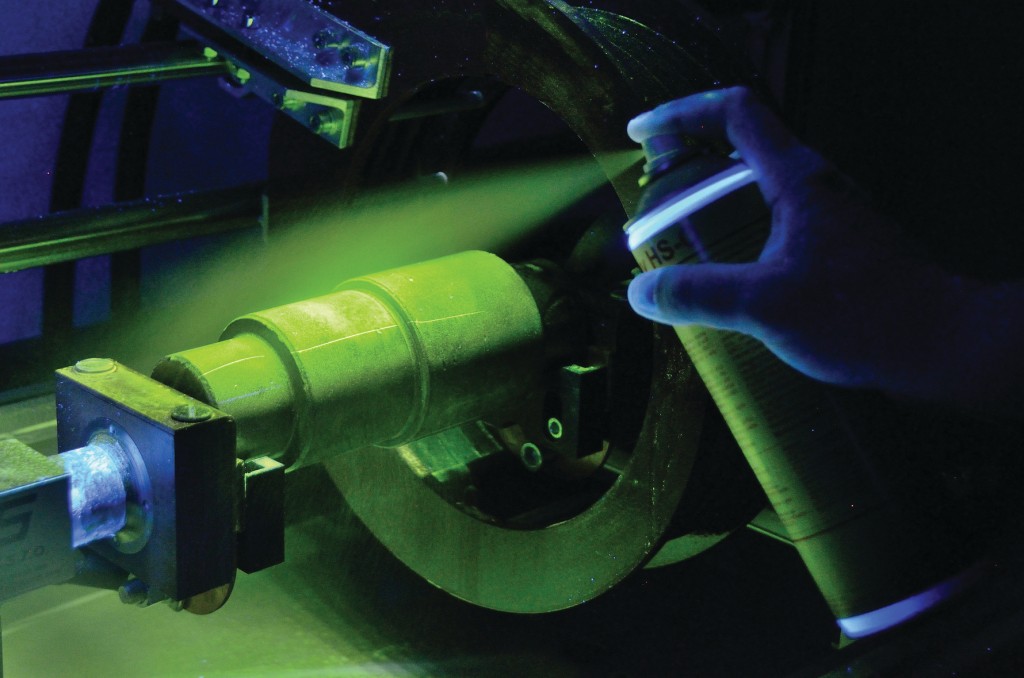
NDT methods for detecting defects on the surface of materials:
- Magnetic particle testing (MPT/MPI): Detection of surface discontinuities (cracks) and near-surface flaws in ferrous materials.
- Dye penetrant testing (DPT/LPI): Detection of defects in all nonporous materials.
- Visual testing (VT): Determination if the dimensional and quality requirements are met.
- Remote visual testing – Endoscopy: Testing at locations where the human eye cannot access.
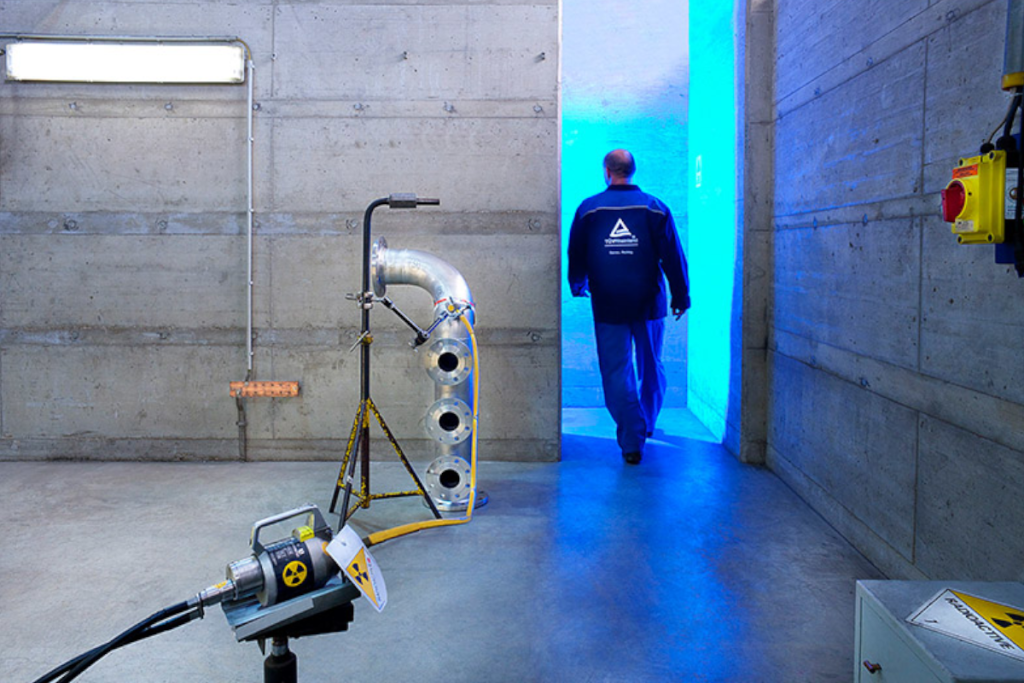
NDT methods for detecting defects inside of materials:
- Radiographic examination of weld (RT): Volumetric inspection of welds and castings for hidden discontinuities and flaws (cracks and voids).
- Ultrasonic examination (UT): Volumetric inspection of welds for hidden discontinuities reliable for detecting lack of fusion and cracks.
- Vacuum box leak testing on storage tank floors: For detection of leakages in welds.

NDT methods for material selection and welding:
- Positive material identification (PMI): Determination if the materials used are in accordance with the specifications.
- Hardness testing: Determination if hardness is within specification after welding or heat treatment.
|
|
Inspection optimization: Increase your plant reliability by optimizing your inspections
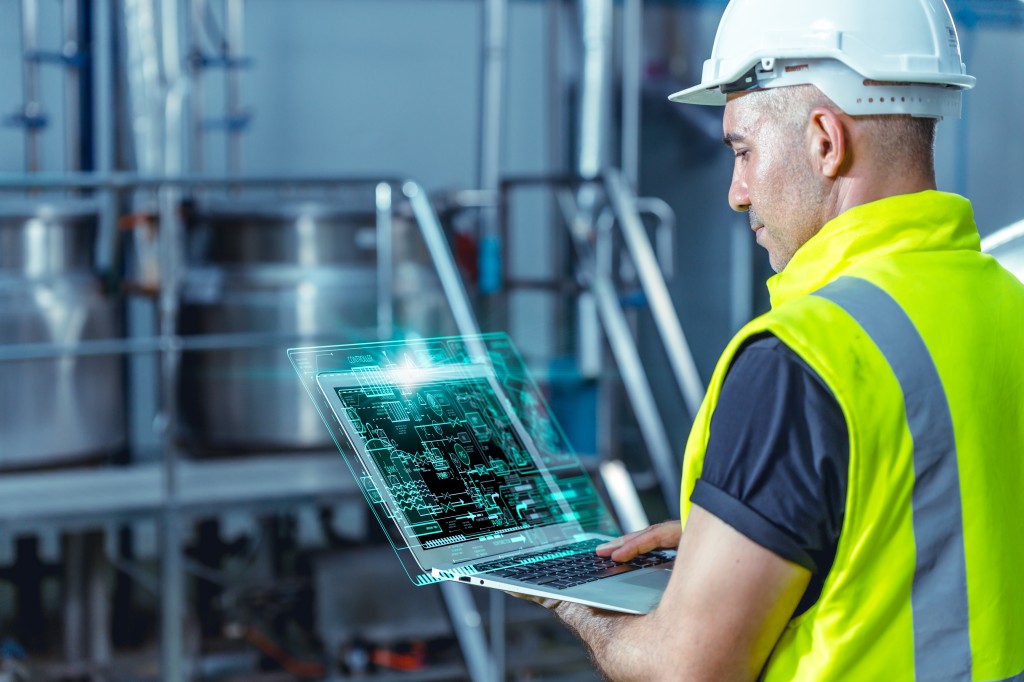
TÜV Rheinland offers optimization services for inspections aimed at enhancing plant reliability and efficiency resulting in the reduction of downtime and unplanned shutdowns.
Tailor-made solutions such as non-intrusive inspections (NII), risk-based inspections (RBI) and Extended Lifetime / Fitness for Service programs target specific damage mechanisms and reduce maintenance costs.
The focus is on using advanced techniques to maintain and ensure plant integrity during operation. With a global network of experts, TÜV Rheinland develops customized strategies to improve the operational safety and viability of your industrial plants.
Contact
