Reduce duration of your scheduled turnarounds and minimize risks of unplanned shutdowns
During a shutdown, the focus is on resuming the production process as quickly as possible while reducing the maintenance costs. Therefore, experienced and skilled workers are needed to identify the present condition of the asset with the help of appropriate (A)NDT methods. The aim is to solve the problem quickly and cost-efficiently, so that the production can re-start as soon as possible.
Overcome specific challenges during the plant shutdowns
Asset owners and operators face special challenges during the shutdown phase because the production has been stopped and the critical equipment should be inspected and repaired accordingly. Here are the common key challenges for plant owners and operators:
The longer the plant is shut down, the higher is the loss of production time and output. That is why the goal of asset owners and operators is to resume the production as quickly as possible. The downtime of the equipment can be minimized by optimal planning of the shutdown activities. Risk Based Inspection (RBI) approach is commonly used to optimize inspection frequencies and reduce turnaround exposure.
During an unplanned shutdown, the production is stopped unintentionally. Any system malfunctions can lead to severe health, safety and environmental (HSE) damages. A good preparation of turnaround activities, including defining the best inspection methods, will help to execute the minimum number of inspections giving the highest level of detection of the weak points and in-service defects, thus reducing the risks of incidents and unplanned shutdowns.
- Performing any inspection from inside of a vessel adds significant Health and Safety risks and requires extra preparation and management costs.
- Performing any inspection from inside of a vessel adds significant Health and Safety risks and requires extra preparation and management costs. Performing Non Intrusive Inspection (NII) could resolve this challenge.
- Avoiding unnecessary draining, purging and cleaning of the vessels, which do not require maintenance, will help improving sustainability targets.
- Uncontrolled shutdowns may lead to a reputational damage of the corporate brand and high additional
payments due to financial liability. Apart from a fear of
losing the product and physical assets, the main focus is on ensuring the health of all involved employees and public (e.g. in case of explosion hazards).
In the event of a planned or unplanned shutdown, we help you to resume the production as quickly as possible and to comply with the safety precautions in accordance with the regulations. Therefore, we offer a broad portfolio of conventional and advanced NDT methods, so that you can resume your operations quickly.
Our NDT methods: Enabling continuation of your production by providing time and cost saving inspections
Depending on the expected degradation, geometry, thickness and material type we offer conventional and advanced NDT methods tailored to your needs. Some of the testing is performed on the inner side of an object from inside of a vessel, however some testing can be performed from outside of the vessel using Non Intrusive Inspection (NII) approach. Have a look at the different applications and our full range of inspection techniques:
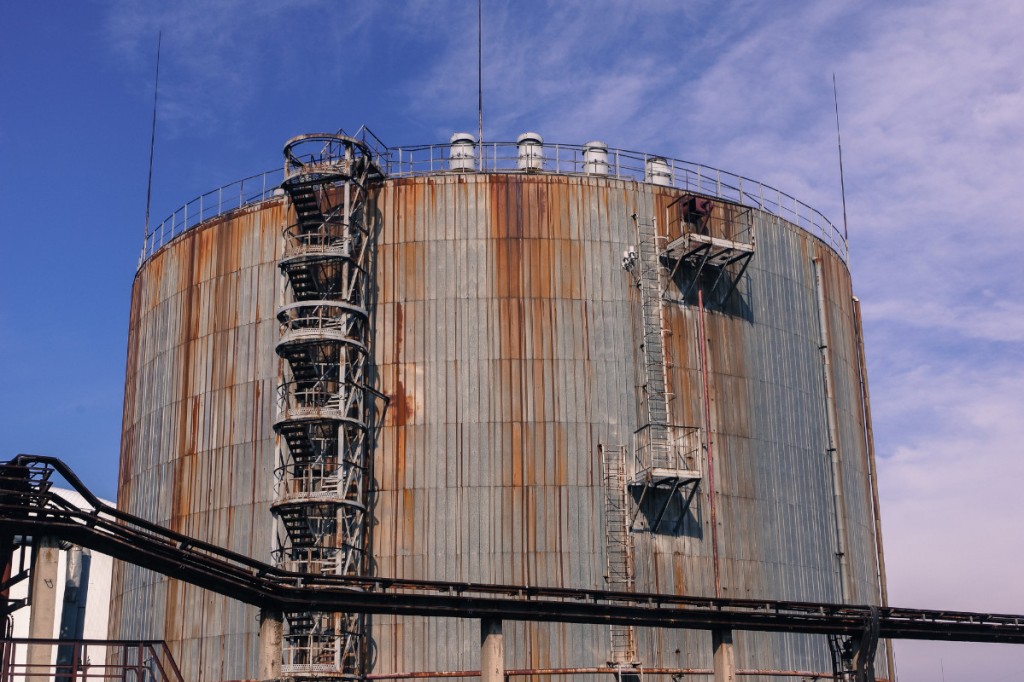
NDT methods for corrosion detection
Corrosion is a problem that affects almost every major industry and can be present in many ways. There are different forms of corrosion such as wall thinning or pitting or Corrosion Under Insulation (CUI). These effects can cause costly repair requirements and safety hazards. What is needed is an effective non-destructive testing inspection plan that detects corrosive anomalies within a shorter timeframe and in a wide range of equipment.
Here is a broad scope of our conventional and advanced NDT methods for corrosion detection:
- Remote visual testing (corrosion, material degradation) using Endoscopy: Determine the quality of components remotely.
- Long Range Ultrasonic Testing (LRUT) / Guided Wave: Detect corrosion and erosion of pipes under insulation.
- Pulsed Eddy Current (PEC): Assess the condition of low carbon steel components by penetrating through insulation and coating layers that are not magnetic and do not conduct electricity (i.e. without removal of insulation or coating).
- Magnetic flux leakage (MFL): Detect corrosion and pitting in steel structures by magnetizing the material (e.g. storage tanks).
- Tank inspections with SLOFEC: Detect small cracks, pitting and general corrosion on both flat and curved surfaces (also double wall tanks).
- Radiographic (RT) examination Gamma-ray (profile inspection): Determine exact thicknesses and detect discontinuities in the material being exposed on the film or digital plate.
- Ultrasonic examination (UT): Accurately determine the thickness of components in order to compare the actual material thickness against the designed or acceptable thickness level.
- Ultrasonic Testing (UT) with crawler: Robotic crawlers provide an easy access to difficult-to-reach components in order to perform UT inspection without a need of scaffolding or access platforms.
- Phased Array (PA) examination of weld (identification): A UT method giving a higher detection rate of volumetric defects and the possibility to save data for reviewing the results at a later time.
- Time of Flight Diffraction (ToFD) examination of weld (sizing): Detect and size depth and height of fusion faults, cracks, etc. in a welded construction independent from their orientation.
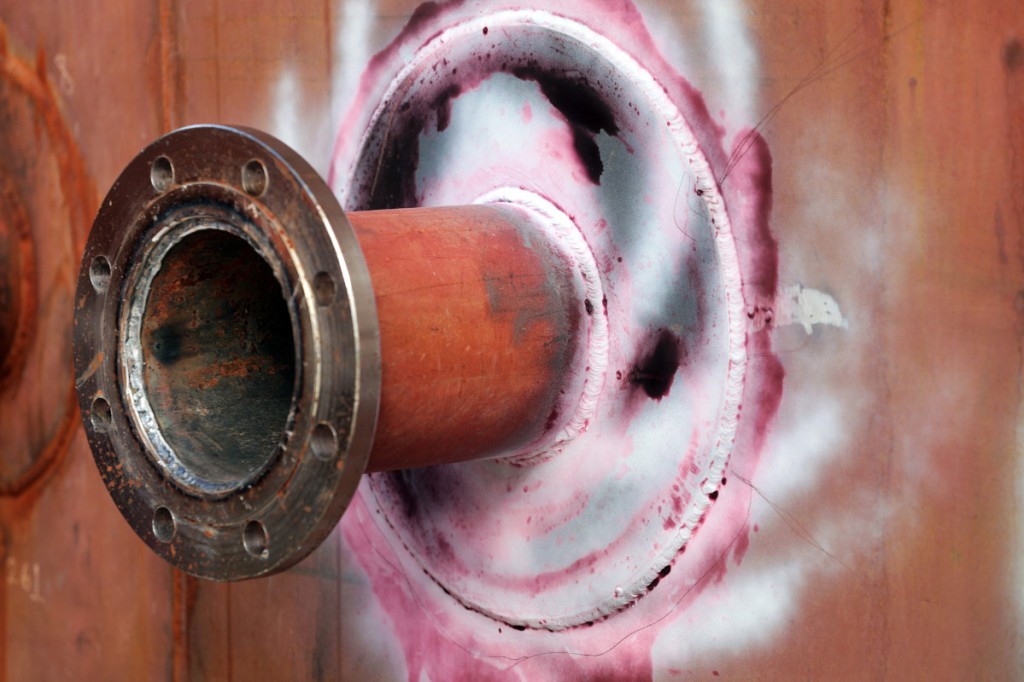
NDT methods for crack and leakage detection and surface damage identification
The crack testing refers to various methods for the detection of cracks and leakages in materials and consequent assessment of safety of the relevant components, e.g. pressure vessels, pipes and components of the petrochemical, process or gas industry. Surface methods are used to identify surface and near surface defects such as cracks and surface porosity. Even seemingly minor surface defects, if they are not addressed quickly enough, can for instance result in widespread damage to any piping network. As such, regular NDT is needed to ensure asset integrity and prevent accidents.
We provide the following methods to detect possible cracks, leakages and surface damages:
- Alternating Current Field Measurement (ACFM): Detect cracks through painting or coating (widely used for subsea underwater inspections).
- Magnetic particle testing (MPT/MPI): Detect discontinuities in ferrous materials.
- Dye penetrant testing (DPT/LPI): Locate surface-breaking defects in nonporous materials.
- Vacuum box leak testing on storage tank floors: Detect the location of leaks.
- Acoustic emission testing (AET): Detect growing metal deformations, cracks, defects and active corrosion at an early stage.
- Phased Array (PA) examination of weld (identification): A UT method giving a higher detection rate of volumetric defects and the possibility to save data for reviewing the results at a later time.
- Time of Flight Diffraction (ToFD) examination of weld (sizing): Detect and size depth and height of fusion faults, cracks, etc. in a welded construction independent from their orientation.
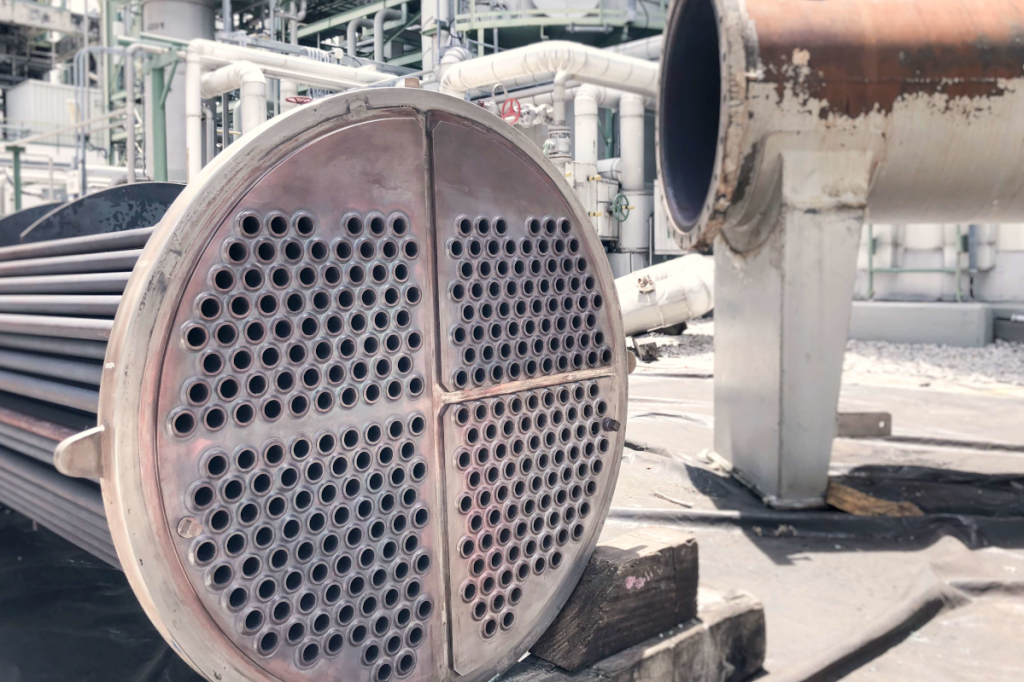
NDT methods for inspection of heat exchanger and furnace piping
In order to maintain heat exchanger tubes in optimum condition, regular non-destructive testing is crucial for the detection of flaws that may lead to a poor heat transfer and increased operating costs. Routine inspection not only helps to avoid sudden failures, but it can also help extending the life of your tubular heat exchangers.
We provide the following NDT methods for inspection of heat exchangers:
- Remote field electromagnetic testing (RFET) - Eddy Current: Detect very small cracks in conductive material.
- Internal rotary inspection system (IRIS): Determine the thickness of tubes by flooding them and inserting a transducer inside of the tube.
- In-Line Inspection (ILI) with Ultrasonic sensors: Detect corrosion and deformation of the pipeline and process piping by sending a special probe (intelligent pig) inside of the pipe.
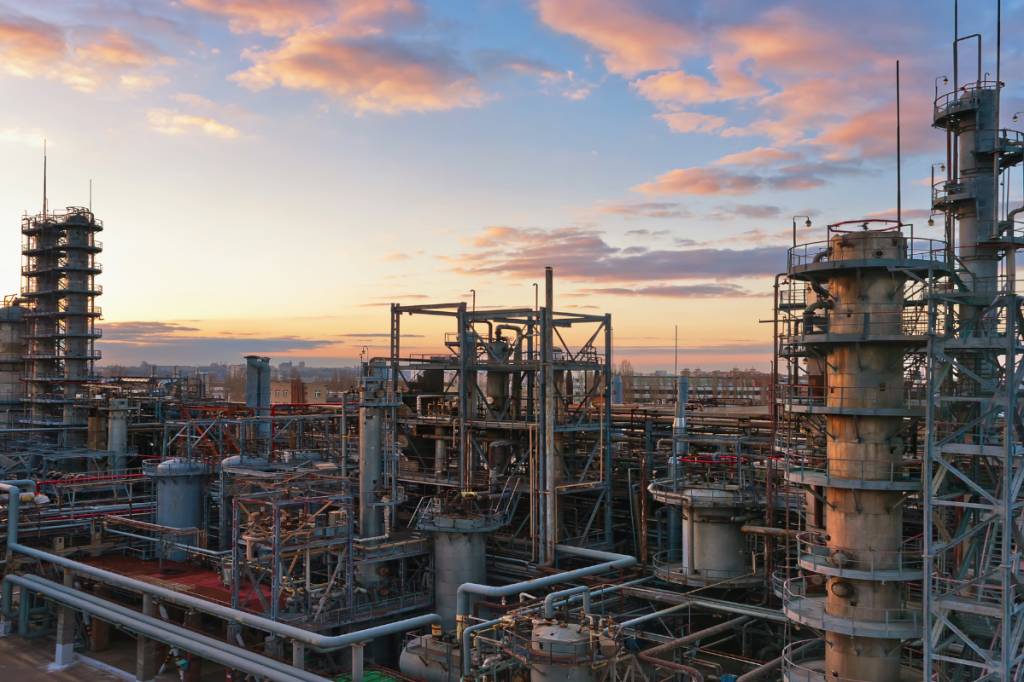
NDT methods for High Temperature Hydrogen Attack inspection
Due to the presence of hydrogen, in combination with high temperature and pressure, the phenomenon of a high temperature hydrogen attack (HTHA) can occur within vessels and piping, making plants and systems susceptible to damage.
Once the risk of HTHA presence is established, it is critical to inspect the equipment for any signs of HTHA. At the early stage of HTHA development, it might be difficult to predict its progression. If the suspected damage is already present, the progression speed might accelerate, for example due to changes in the process. Therefore, it is always desirable to detect HTHA as early as possible and to monitor its development more frequently.
It is very difficult to detect HTHA damage at early stages of its development. The latest industry recommendation is to use a combination of Advanced NDT techniques:
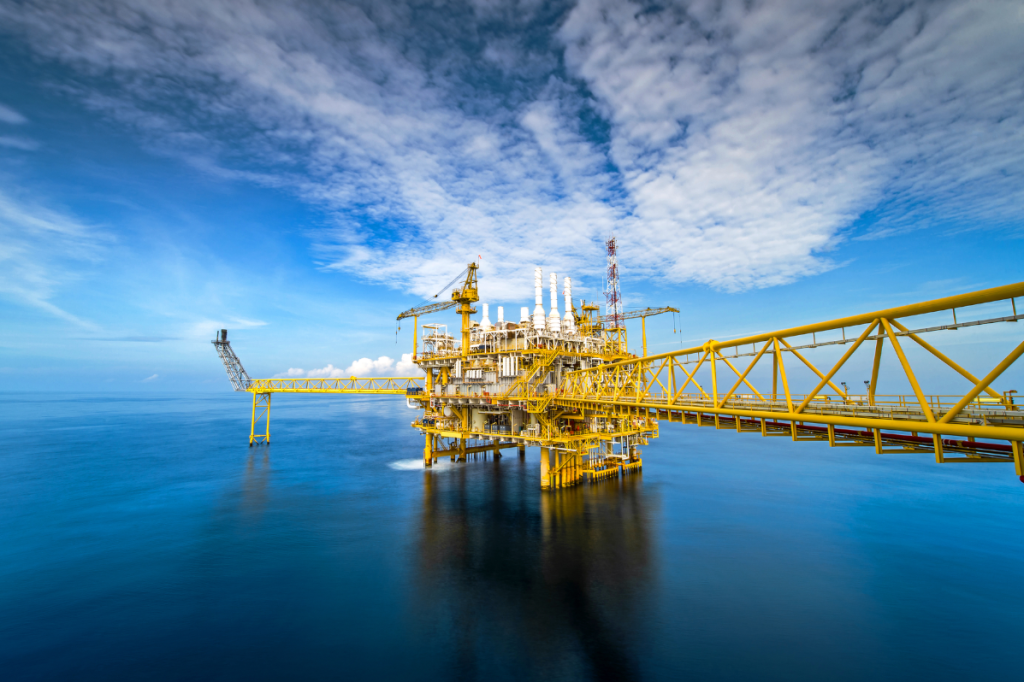
NDT methods for material loss logging (offshore well inspection)
When assessing the condition of the offshore well casings and conductors using NDT, it is necessary to accurately characterize hidden corrosion by identifying the affected layers, and measuring both the amount of metal loss and the associated pillowing due to the corrosion process. TÜV Rheinland has developed a unique inspection method for the offshore industry:
Inspection optimization: Increase your plant reliability by optimizing your inspections
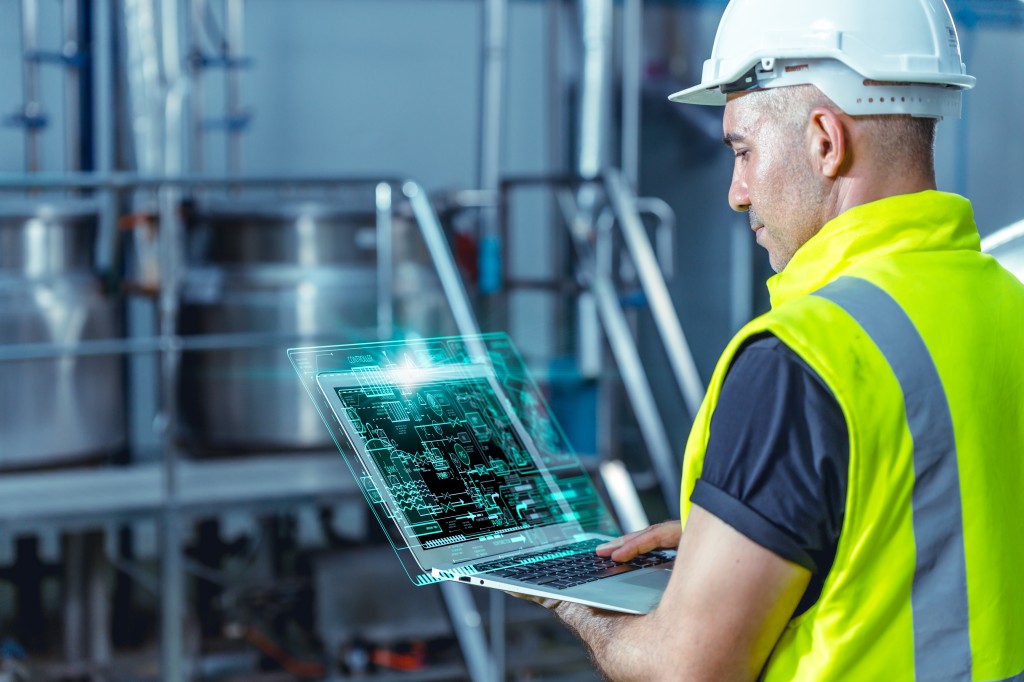
TÜV Rheinland offers optimization services for inspections aimed at enhancing plant reliability and efficiency resulting in the reduction of downtime and unplanned shutdowns.
Tailor-made solutions such as non-intrusive inspections (NII), risk-based inspections (RBI) and Extended Lifetime / Fitness for Service programs target specific damage mechanisms and reduce maintenance costs.
The focus is on using advanced techniques to maintain and ensure plant integrity during operation. With a global network of experts, TÜV Rheinland develops customized strategies to improve the operational safety and viability of your industrial plants.
Contact
