Zerstörungsfreie Prüfung (ZfP) bei Anlagenstillstand
Bei einem Betriebsstillstand kommt es darauf an, den Produktionsprozess so schnell wie möglich wieder aufzunehmen und gleichzeitig die Wartungskosten zu senken. Daher werden erfahrene und qualifizierte Arbeitskräfte benötigt, die den aktuellen Zustand einer Anlage mit Hilfe geeigneter (erweiterten) ZfP-Methoden ermitteln. Ziel ist es, das Problem schnell und kosteneffizient zu beheben, damit die Produktion so schnell wie möglich wieder aufgenommen werden kann.
Überwindung spezifischer Herausforderungen während des Stillstands von Anlagen
Anlagenbesitzer und -betreiber stehen während der Phase der Abschaltung einer Anlage vor besonderen Herausforderungen, da die Produktion gestoppt wurde und die betreffenden Anlagen entsprechend inspiziert und repariert werden müssen. Nachfolgend sind die wichtigsten Herausforderungen für Anlagenbesitzer und -betreiber aufgeführt:
Je länger eine Anlage abgeschaltet ist, desto höher ist der Verlust an Fertigungszeit und Produktionsleistung. Deshalb ist es das Ziel von Anlagenbesitzern und -betreibern, die Produktion so schnell wie möglich wieder aufzunehmen. Die Ausfallzeiten von Anlagen lassen sich durch eine optimale Planung der Maßnahmen, die während des Stillstands zu ergreifen sind, minimieren. Der Ansatz einer risikobasierten Inspektion (RBI) wird oft angewandt, um die Häufigkeit von Inspektionen zu optimieren und die Anzahl der Stillstände zu verringern.
Bei einem ungeplanten Stillstand wird die Produktion unbeabsichtigt angehalten. Jede Systemstörung kann zu schwerwiegenden Gesundheits-, Sicherheits- und Umweltschäden führen. Eine gute Vorbereitung der während des Stillstands zu ergreifenden Maßnahmen, einschließlich der Festlegung der optimalen Inspektionsmethoden, sorgt dafür, dass so wenig Inspektionen wie möglich durchgeführt werden müssen, um so viele Schwachstellen und Betriebsdefekte wie möglich aufzuspüren und somit das Risiko von Zwischenfällen und ungeplanten Stillständen zu verringern.
- Jede Inneninspektion eines Lagerbehälters stellt ein erhebliches Gesundheits- und Sicherheitsrisiko dar und erfordert zusätzliche Vorbereitungs- und Verwaltungskosten. Die Durchführung von nicht-invasiven Inspektionen (NII) kann hier Abhilfe schaffen.
- Die Vermeidung einer unnötigen Leerung, Spülung und Reinigung von Lagerbehältern, die am Ende nicht gewartet werden müssen, verbessert die Nachhaltigkeitsziele.
- Unkontrollierte Stillstände können den Ruf des Unternehmens schädigen und haftungsbedingte hohe zusätzliche finanzielle Verluste nach sich ziehen. Neben der Sorge um den Verlust von Produkt und Anlagen liegt das Hauptaugenmerk auf dem Schutz der Gesundheit aller beteiligten Mitarbeitenden und der Öffentlichkeit (z. B. bei Explosionsgefahr).
Im Falle eines geplanten oder ungeplanten Stillstandes helfen wir Ihnen, die Produktion so schnell wie möglich wieder aufzunehmen und die Sicherheitsvorschriften gemäß den gesetzlichen Bestimmungen einzuhalten. Zu diesem Zweck bieten wir ein breites Portfolio an herkömmlichen und erweiterten ZfP-Methoden an, damit Sie den Betrieb Ihrer Anlagen schnell wieder starten können.
Unsere ZfP-Methoden: Zeit und Kosten sparende Inspektionen zur Aufrechterhaltung Ihrer Produktion
Je nach zu erwartendem Verschleiß sowie der Geometrie, der Dicke und der Materialart bieten wir herkömmliche und erweiterte ZfP-Methoden an, die auf Ihre speziellen Bedürfnisse zugeschnitten sind. Einige der Prüfungen werden im Inneren eines Lagerbehälters oder an der Innenseite eines Objekts durchgeführt, andere Prüfungen können jedoch auch von außerhalb des Behälters mit Hilfe von nicht-invasiven Inspektionen (NII) durchgeführt werden. Nachfolgend sind die verschiedenen Anwendungen und unser komplettes Angebot an Prüfmethoden aufgeführt:
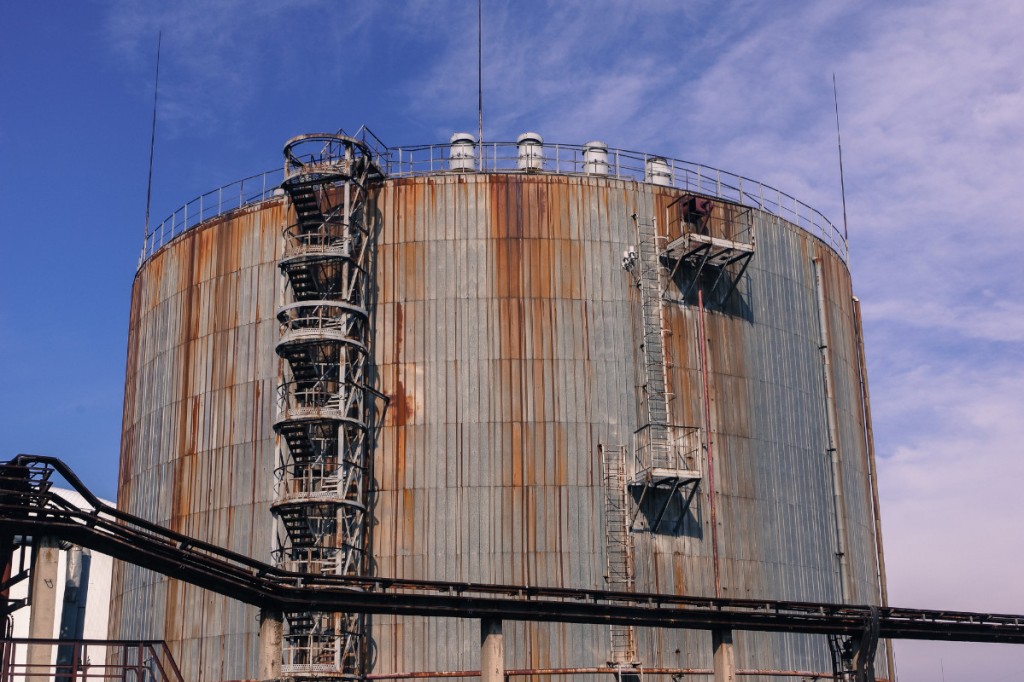
ZfP-Methoden zur Korrosionserkennung
Korrosion ist ein Problem, von dem fast alle großen Industriezweige betroffen sind und das sich auf vielfältige Weise manifestieren kann. Es gibt verschiedene Formen von Korrosion, wie z. B. Wandverdünnung, Lochfraß oder Korrosion unter der Isolierung (CUI). Diese Erscheinungen können kostspielige Reparaturen erforderlich machen und ein Sicherheitsrisiko darstellen. Gefragt ist ein effektiver Plan für zerstörungsfreie Prüfungen, mit dem korrosive Anomalien innerhalb eines kürzeren Zeitraums und bei einer Vielzahl von Anlagen ermittelt werden können. Nachfolgend finden Sie einen umfassenden Überblick über unsere herkömmlichen und erweiterten ZfP-Methoden zur Korrosionserkennung:
- Remote-Prüfung (Korrosion, Materialverschleiß): Bestimmung der Qualität von Komponenten aus der Ferne.
- Langstrecken- Ultraschallprüfung (LRUT)/Guided Wave Testing (GWT): Erkennung von Korrosion und Erosion von Rohren unter der Isolierung.
- Wirbelstromprüfung (PEC): Beurteilung des Zustands von Bauteilen aus kohlenstoffarmem Stahl durch Durchdringung von Isolierungen und Beschichtungen, die nicht magnetisch sind und keinen Strom leiten (d. h. ohne Entfernung der Isolierung oder Beschichtung).
- Magnetische Streuflussprüfung (MFL): Ermittlung von Korrosion und Lochfraß in Stahlkonstruktionen durch Magnetisierung des Materials (z. B. Lagertanks).
- Behälterinspektionen mit SLOFEC: Erkennung von kleinen Rissen, Lochfraß und genereller Korrosion sowohl auf flachen als auch gekrümmten Oberflächen (inkl. Doppelwandtanks).
- Durchstrahlungsprüfung (RT), Gammastrahlen (Profilprüfung): Bestimmung der genauen Dicke und Erkennung von Unregelmäßigkeiten im Material, die auf Film oder einen digitalen Detektor übertragen werden.
- Ultraschallprüfung (UT): Genaue Bestimmung der Dicke von Bauteilen, um die tatsächliche Materialdicke mit der konzipierten bzw. zulässigen Dicke zu vergleichen.
- Ultraschallprüfung (UT) mit Roboterfahrzeug: Roboterfahrzeuge ermöglichen den Zugang zu schwer zugänglichen Bauteilen, um UT-Prüfungen durchzuführen, ohne Gerüste oder Zugangsplattformen zu benötigen.
- Phased-Array Ultraschallprüfung (PAUT) von Schweißnähten: Eine Ultraschallmethode, die eine bessere Erkennung von volumetrischen Defekten erlaubt und die Möglichkeit bietet, Daten zu speichern, um die Ergebnisse zu einem späteren Zeitpunkt zu überprüfen.
- Ultraschallprüfung mit Beugungsleufzeittechnik TOFD (Time of Flight Diffraction) zur Prüfung von Schweißnähten: Erkennung und Bestimmung der Tiefe und Größe von Schweißfehlern, Rissen usw. in einer geschweißten Konstruktion unabhängig von deren Ausrichtung.
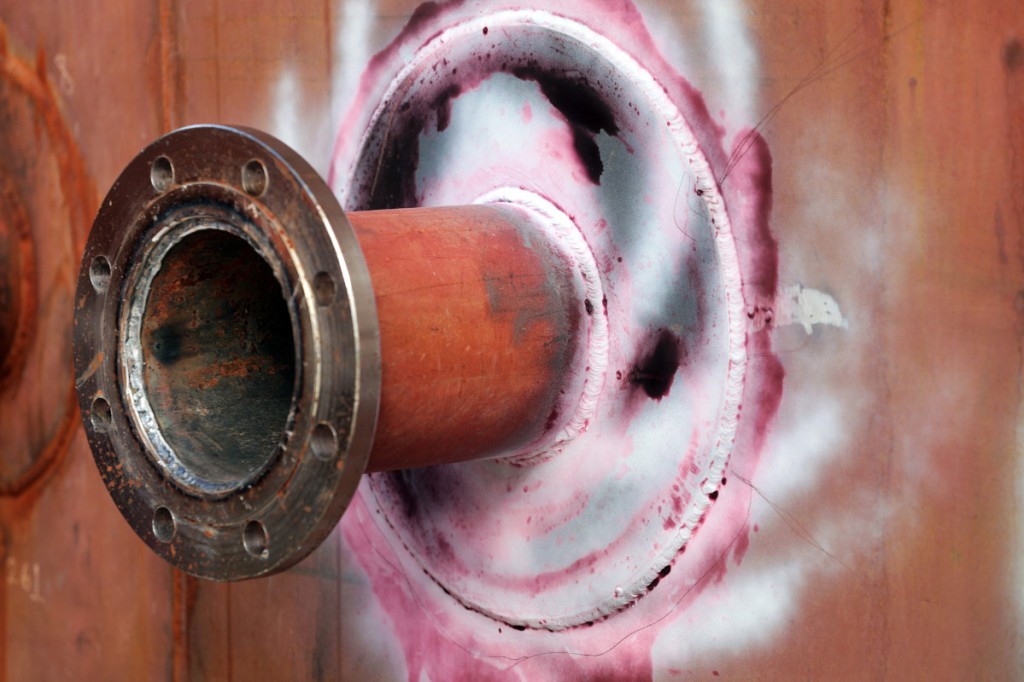
ZfP-Methoden zur Ortung von Rissen und Leckagen und zur Erkennung von Oberflächenschäden
Unter einer Rissprüfung versteht man verschiedene Methoden zur Erkennung von Rissen und Leckagen in Werkstoffen und die daraus resultierende Beurteilung der Sicherheit der betreffenden Bauteile, z. B. von Druckbehältern, Rohren und Komponenten in der petrochemischen, Prozess- oder Öl- & Gasindustrie. Oberflächenmethoden werden eingesetzt, um Oberflächendefekte und oberflächennahe Fehler wie Risse und Oberflächenporosität zu erkennen. Selbst scheinbar kleine Oberflächenfehler können, wenn sie nicht rechtzeitig repariert werden, zu großen Schäden in einem Rohrleitungsnetz führen. Daher ist eine regelmäßige ZfP erforderlich, um die Integrität der Anlage zu gewährleisten und Unfälle zu vermeiden. Wir bieten die folgenden Methoden zur Erkennung von Rissen, Leckagen und Oberflächenschäden an:
- Wechselstrom-Feldmessung (ACFM): Erkennung von Rissen in Anstrichen, Lackierungen oder Beschichtungen (häufiger Einsatz bei Unterwasserinspektionen).
- Magnetpulverprüfung (MT): Erkennung von Unregelmäßigkeiten in ferromagnetischen Materialien.
- Eindringprüfung (PT): Ortung von Oberflächendefekten in nicht porösen Materialien.
- Vakuum-Dichtheitsprüfung an Lagertankböden: Ortung von undichten Stellen.
- Schallemissionsprüfung (AT): Erkennung von fortschreitenden Metallverformungen, Rissen, Korrosion und Defekten in einem frühen Stadium.
- Phased-Array Ultraschallprüfung (PAUT) von Schweißnähten: Eine Ultraschallmethode, die eine bessere Erkennung von volumetrischen Defekten erlaubt und die Möglichkeit bietet, Daten zu speichern, um die Ergebnisse zu einem späteren Zeitpunkt zu überprüfen.
- Ultraschallprüfung mit Beugungslaufzeittechnik TOFD (Time of Flight Diffraction) zur Prüfung von Schweißnähten: Erkennung und Bestimmung der Tiefe und Größe von Schweißfehlern, Rissen usw. in einer geschweißten Konstruktion unabhängig von deren Ausrichtung.
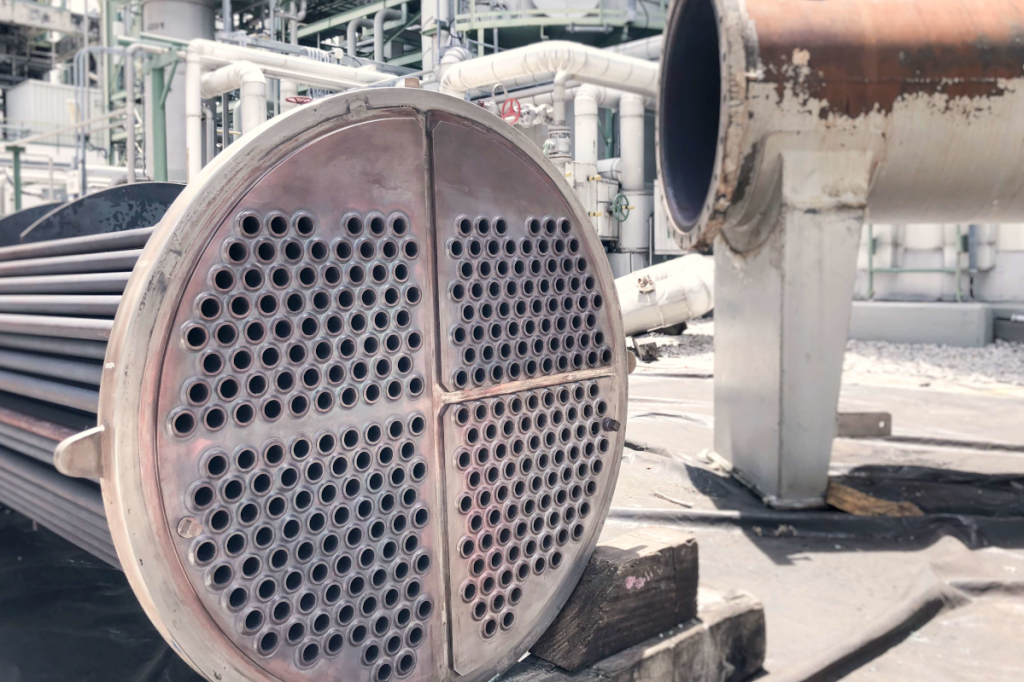
ZfP-Methoden zur Inspektion von Wärmetauscher und Heizungsrohren
Um die Rohre von Wärmetauschern in einem optimalen Zustand zu halten, ist eine regelmäßige zerstörungsfreie Prüfung unerlässlich, damit Mängel aufgedeckt werden, die zu einer schlechten Wärmeübertragung und zu erhöhten Betriebskosten führen können. Eine routinemäßige Inspektion hilft nicht nur, plötzliche Ausfälle zu vermeiden, sondern kann auch die Lebensdauer Ihrer Röhrenwärmetauscher verlängern. Wir bieten die folgenden ZfP-Methoden für die Prüfung von Wärmetauschern an:
- Elektromagnetische Fernfeldprüfung – Wirbelstromprüfung (ET): Erkennung sehr kleiner Risse in leitfähigem Material.
- Internes Rotationsprüfsystem (IRIS): Bestimmung der Dicke von Rohren durch Fluten und Einführen eines Prüfkopfes in das Rohr.
- Inline-Inspektion (ILI) mit Ultraschallsensoren: Erkennung von Korrosion und Verformungen von Rohr- und Prozessleitungen durch Einführen einer speziellen Sonde (intelligenter Molch) in das Innere des Rohrs.
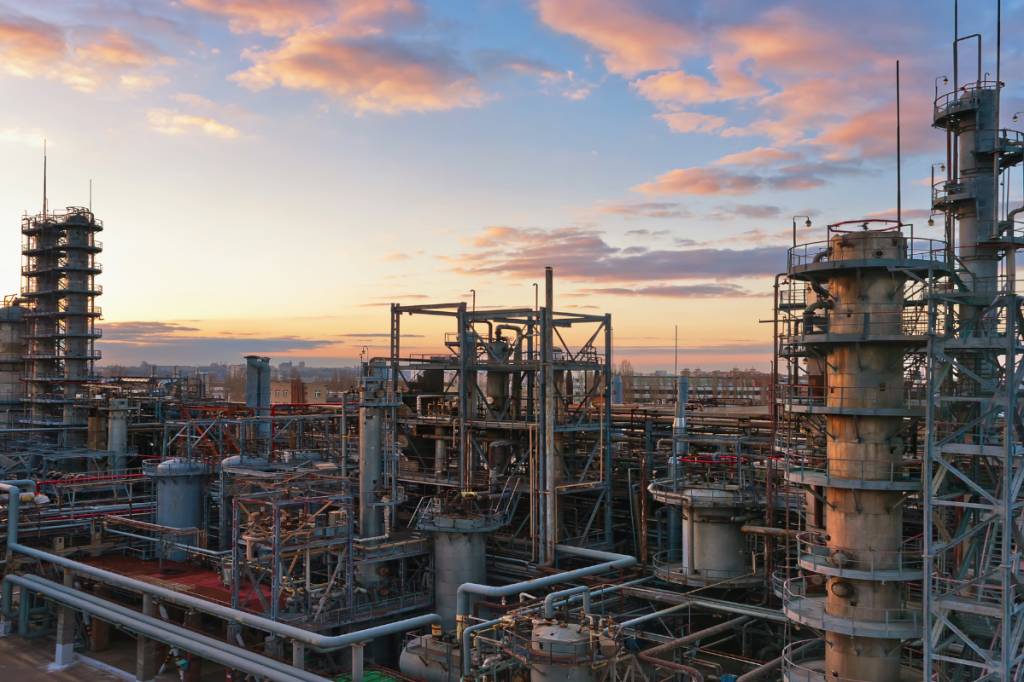
ZfP-Methoden für die Prüfung von Hochtemperatur-Wasserstoffangriffen (HTHA)
Durch das Vorhandensein von Wasserstoff in Kombination mit hohen Temperaturen und Druck kann es in Behältern und Rohrleitungen zu einem Hochtemperatur-Wasserstoffangriff (engl. High Temperature Hydrogen Attack, HTHA) kommen, was Anlagen und Systeme anfällig für Schäden macht.
Sobald das Risiko des Auftretens eines HTHA festgestellt wird, ist es wichtig, die Anlagen auf Anzeichen von HTHA zu überprüfen. Im Frühstadium der Entwicklung eines HTHA ist es oft schwierig, das Voranschreiten des Schadens vorherzusagen. Ist der vermutete Schaden bereits vorhanden, kann sich das Fortschreiten beispielsweise aufgrund von Änderungen im Verfahren beschleunigen. Daher ist es immer erstrebenswert, einen HTHA so früh wie möglich zu erkennen und seine Entwicklung engmaschig zu überwachen.
Es ist sehr schwierig, HTHA-Schäden in den frühen Stadien ihrer Entwicklung zu erkennen. Die aktuelle Empfehlung der Industrie beinhaltet den Einsatz einer Kombination erweiterter ZfP-Methoden:
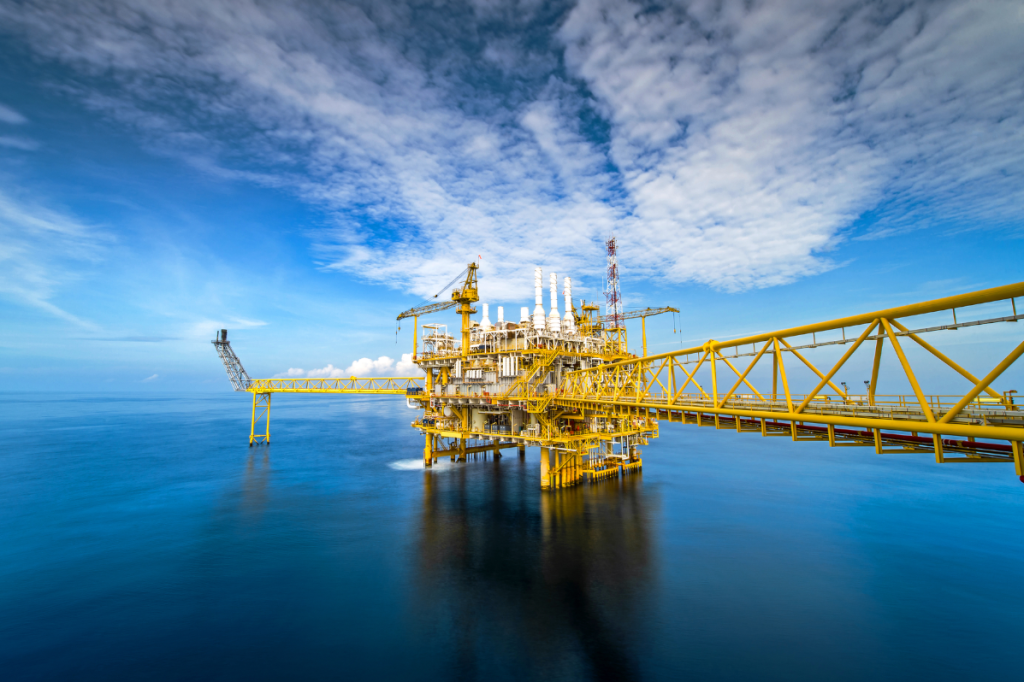
ZfP-Methoden zur Erfassung von Materialverlusten (Offshore-Bohrlochinspektion)
Bei der Beurteilung des Zustands von Offshore-Bohrlochverkleidungen und -leitungen mit Hilfe von ZfP ist es notwendig, versteckte Korrosion genau zu charakterisieren. Dazu müssen die betroffenen Schichten identifiziert und sowohl das Ausmaß des Metallverlusts als auch das damit verbundene korrosionsbedingte Pillowing gemessen werden. TÜV Rheinland hat eine spezielle Prüfmethode für die Offshore-Industrie entwickelt:
